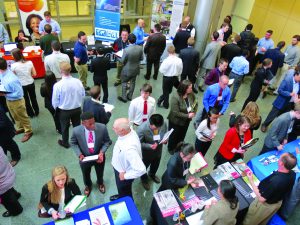
TEC’s career fair emphasizes the importance of collaborative and interactive approaches to biopharmaceutical training and industry education. (www.btec.ncsu.edu)
As in most high-tech sectors, success within the highly regulated biopharmaceutical manufacturing industry depends upon an adaptable, skilled, educated, and high-performing workforce. The impact of human performance cuts across the entire industry — whether for a manufacturing operator, a scientist or engineer in a highly technical role such as process development, or a technical sales representative serving the industry.
The effects of poor performance can be seen easily in deviation reports and FDA warning letters as well as in quantified productivity metrics surrounding time to proficiency, yield, revenue, employee engagement, and retention. Although many factors influence human performance, a lack of appropriate training is far too often cited as a root cause.
Further, new technologies are creating potentially disruptive changes within the industry, including applying single-use technologies and continuous processing; implementing quality by design (QbD) principles and process analytical technology (PAT); and introducing new therapies and personalized medicine. In response, education and technical professional development are critical to ensuring that the competency level of today’s biopharmaceutical manufacturing workforce grows as the industry evolves.
Although the motivators, stakeholders, and end goals vary by learning endeavor, a robust training program needs to rely on a variety of training resources. Those include strong internal training programs on both quality and current good manufacturing practice (CGMP) and manufacturing/technical topics; industry-specific training centers; universities, community colleges, and professional societies; and the industry’s large number of suppliers.
A Highly Skilled Workforce Necessitates Learning Investment
The biopharmaceutical manufacturing workforce is highly skilled, educated, and technical in nature. Regardless of functional role or educational background, people working within the industry share a common technical lexicon and the same regulatory framework. Because the FDA and international regulators govern all aspects of the business, working in this environment requires a learned mind-set shared by employees and suppliers, regardless of job function.
Yet despite a common language and regulatory framework, the workforce is diverse with respect to both background and job function. From the engineers and diverse network of suppliers and consultants designing facilities and equipment to the technicians ensuring that product quality is not compromised, there are many different job functions, educational pathways into the industry, and a diverse array of productivity and performance metrics that define success.
Many of these skills, technologies, and processes are unique to the industry, so career growth and success will hinge on individuals, departments, and organizations engaging in learning and development opportunities.
A Paradigm Change in Biopharmaceutical Education
When it comes to company-driven training programs in biopharmaceutical manufacturing, the industry has historically trained people with a focus on compliance and on demonstrating to regulatory agencies that personnel are trained to perform tasks effectively. As a result, training departments have devoted countless hours to proper tracking and documentation of staff training events and less time on content and methods of delivery.
For many companies, training largely has consisted of reading relevant standard operating procedures (SOPs) and completing relevant “on-the-job” training. Yet like most technology-based industries, the biopharmaceutical manufacturing industry has changed dramatically in our postrecession world. Companies are placing greater importance on an individual’s ability to contribute to organizational efficiency, be mindful of ways to save costs, and generate good business results.
The training paradigm within the biopharmaceutical industry is changing as well. We now see biopharmaceutical companies examining learning and development best practices from other industries. Ben Locwin is the global head of R&D learning at Biogen. Having worked as a consultant in the nuclear power, automobile, and aerospace industries, Ben presented the following reflections in conversation:
Industries that have catastrophic error potential (such as the nuclear power industry, aerospace, and so forth) have quickly tried to get to a position of training staff in a practical way. Work is actually performed to build the mental connection between task-related learning intervention and actual work practice.
Defects in the nuclear power industry have decreased in some cases more than 90% from what they were a little over two decades ago. Although it’s fashionable to jump right to the mental shorthand of “nuclear” as an industry to model ours after, I also have worked on the design of these enhanced training approaches in the aerospace, automotive, and food and beverage industries. In some cases, the catastrophic potential also can be very high (such as having contaminated product reach store
shelves for consumers) or having personnel who are under- or untrained working on a production line where dismemberment or death is possible (and they do occur, as I have seen).
Think about the significant market share that Chipotle lost — for a long time now — because of what amounts largely to food-handling and preparation-training practices. And with public scrutiny already on the pharmaceutical industry for drug price hikes, it won’t take much more to exceed a tipping point and have public perception lead to tremendous pressures and shifts. (1)
Companies are indeed shifting — moving away from models in which training is solely a compliance-driven activity to one in which training is driven by performance, efficiency, and business goals. This change comes just in time and will be ever more critical as companies strive to adopt, adapt, and grow in response to new and emerging technologies.
A Rapidly Changing Industry Demands New Expertise
The biopharmaceutical manufacturing industry is changing rapidly. With an array of potentially game-changing innovations to products, processes, and analytical techniques, unique learning and development needs must be addressed. Below are listed a few of these trends, innovations, and factors that will necessitate training.
New Technologies: In the past several years, single-use technologies have grown from being a mere buzzword to a transformative technology. Most leading biopharmaceutical manufacturers are integrating such technologies into their processes. Coupled with the increasing level of automation, PAT, electronic batch record systems, new analytical methods, and the promise of continuous processing, technological advances have an impact on most functional areas within the industry (as shown in the “Technology Changes” box). Successful evaluation, selection, and implementation of such technologies hinges on properly educated business and technical leaders with up-to-date scientific understanding.
Technology Changes
The following changes in technology require increased knowledge and skill: |
Process Development
|
Manufacturing
|
Quality Control
|
Quality Assurance/Regulatory
|
Emerging Therapies: Therapeutic proteins, monoclonal antibodies (MAbs), and vaccines have been the mainstay of biologics manufacturing. Yet technological and regulatory changes have driven progress in commercialization of transformative new types of therapies including biosimilars, antibody–drug conjugates (ADCs), and gene and cell-based therapies as well as the emerging promise of personalized medicine. Developing a workforce that is familiar with these new product types, processes, and regulations will be critical as suppliers, existing manufacturing companies, and emerging companies venture in new directions.
Increasing Supplier Integration: The relationship between the biopharmaceutical manufacturing industry and its suppliers has changed as well. Fueled by business and regulatory challenges, suppliers have moved away from a purely transactional business model to one that is service-oriented and far more interdependent with biomanufacturers. As noted by the Biophorum Operations Group (BPOG) in its 2016 report,
Teamwork between suppliers and end users is widely acknowledged as crucial to solving systemic and cultural challenges in the industry, particularly around compliance, control, and efficiency challenges. Close-coupled, integrated, transparent, end-to-end supply chain management is gaining widespread understanding and support. (2)
Successful partnership requires supply-side sales, marketing, and field application teams that have an ever-increasing understanding of how CGMP requirements and expectations are translated into practice at pilot and commercial scale (2).
Evolution of a “Gig” Economy: Fifty years ago, people left college and launched a career — often staying in the same company until they retired many years later. Yet the paradigm is different today as individuals change companies, change jobs, and more and more organizations contract in size and increase productivity by relying on highly skilled independent contractors for fixed-duration engagements.
A recent study by Intuit predicts that “in the [United States] alone, contingent workers will exceed 40% of the workforce by 2020” (3). In addition to driving a need for enhanced communication and project management skills at many levels in the organization, this growing reliance on a temporary workforce will necessitate efficiency across learning and development programs.
Globalization: As companies have become more global and supply chains integrate, the culture of work continues to evolve as technicians, contractors, corporate leadership, and suppliers work side-by-side across large geographic terrains on multiple projects simultaneously. The industry needs employees with not only the scientific and technical knowledge to perform jobs, but also the professional, communication, business, and global regulatory awareness to thrive in today’s cross-functional and highly matrixed work environment.
Both formal and informal learning and development approaches play a large role in the adoption of new technologies, processes, and business cultures within organizations. In planning to raise the technical, regulatory, and professional competency of its workforce, leaders in the biopharmaceutical industry should proactively look to both internal and external learning and development partners to help catalyze positive change.
Leveraging Internal and External Learning Partners
With new process and analytical technologies, therapies, regulations, and business processes propelling the biomanufacturing industry forward, business and technical managers must remain cognizant of the requisite knowledge, skill, and competency of their personnel at all levels. In working to assess and develop their workforce, companies should consider leveraging both internal and outsourced resources to meet learning and development objectives.
Both internal and outsourced solutions play a vital role in talent development. Based on the Association of Talent Development’s 2015 State of the Industry report, nearly 40% of learning and development expenditures at surveyed companies across multiple industries are used for outsourced solutions (including both external services and tuition reimbursement) (4).
Internal programs are vital to organizational success and comprise the bulk of learning expenditures. That said, it can be challenging to identify resources at some companies when the training function often is distributed across training departments, manufacturing, quality assurance, and human resources, depending on the nature of the content. Although the training function in some organizations is highly evolved and aligned with best practices in other industries, many companies are locked into traditional training modes such as “read and understand.”
External learning and development providers are critical in closing gaps and providing education and training on many new and emerging trends and technologies. A large network of suppliers, service providers, educational institutions, professional associations, and consultants add value. They provide education on foundational scientific concepts as well as technical training on emerging technologies, vendor-specific equipment, and a large array of GMP and compliance-related topics.
In addition, because of strategic regional and national investment in biotechnology economic and workforce development, a growing number of industry-specific instructional centers and a growing number of university and community college academic and professional development programs are focused on biopharmaceutical manufacturing.
Effective Educational Partnerships Generate Value
Depending on specific learning challenges and the envisioned business impact, external learning and development partnerships offer a mechanism to motivate, educate, and upskill segments of a workforce in response to a changing industry.
A recent partnership between French multinational pharmaceutical manufacturer Sanofi and the Biomanufacturing Training and Education Center (BTEC) located at North Carolina State University offers an example of effective partnership. With biologics and vaccine manufacturing distributed broadly in nearly every region of the world, Sanofi relies upon its global quality auditing team to ensure that sites operate in accordance with international and Sanofi-specific regulations and guidance documents.
Sanofi reached out to BTEC as part of an internal initiative focused on developing skilled biotechnology professionals. Through an iterative design process, a one-week training program was developed and piloted in 2015 with key business leaders from Sanofi, Sanofi-Pasteur, and Genzyme. The program consisted of about 50% lecture and 50% hands-on training on upstream and downstream unit operations, analytical technologies, and final fill–finish operations in a simulated CGMP environment. The program was refined and rolled out to a group of auditors from the United States, France, China, India, Japan, and the United Kingdom in 2016. The course was a well-received start to a recurring program focused on providing a theoretical, practical, and regulatory grounding for personnel involved in auditing biologics manufacturing sites.
The Sanofi program and similar programs designed for other biomanufacturing companies, their suppliers, and regulatory officials reveal several best practices to help shape effective program development and partnership.
Identify Clear and Discernible Learning Goals Aligned with the Business Need: When beginning discussions with internal or external training partners, it is important that the business need, learning outcomes, and audience are understood by both the client and training provider. Knowing the need and the audience enables instructional designers and subject-matter experts to develop a curriculum with suitable content and depth of coverage.
Ensure That Participants Understand the Goal: Even if a business or technical leader can recognize and articulate the value of a specific learning and development project for the purpose of course design, that vision must be communicated to participants as well. Without their buy-in, initiatives run the risk of failure due to lack of engagement or even boredom, as participants wonder, “Why am I taking this course?”
Leverage the Experiences of Others, but Customize When Necessary: External training providers can develop curricula rapidly by relying on preexisting content, learning modules, and hands-on activity protocols. In making sure that a curriculum is well-aligned with your desired learning outcome, ensure review of content outlines and be sure to suggest modifications or enhancements when appropriate.
Keep Participants Engaged: Participants lose interest sitting in a classroom for eight hours. Learning and development programs should be interactive, participatory, and contain significant practical and hands-on exercises to apply new-found knowledge and skills.
Embrace the Opportunity for Team building: Hands-on education and training experiences do necessitate travel in today’s global workplace. Although the primary goal of most programs is education, don’t ignore the added benefits of team building, employee engagement, and motivation that come along with bringing geographically distributed and field-based teams together.
At the end of the day, well-executed external partnerships can add tremendous value to a company and its personnel. Set against the backdrop of a biopharmaceutical manufacturing industry that is growing and changing rapidly, professional development is no longer a series of isolated events, nor is internal “training” simply a task-oriented, compliance-driven activity.
Continuous, Lifelong Processes
For companies and the industry as a whole to grow and expand, learning and development are becoming continuous and lifelong processes — much as they have been in many other professional circles such as healthcare and information technology. In carefully leveraging a mix of internal and external learning and development partners to understand and address learning challenges, companies can minimize costs and bring outside perspectives, ideas, and subject matter expertise to move their businesses forward.
About the Biomanufacturing Training and Education Center
The Biomanufacturing Training and Education Center (BTEC) is located at NC State University’s Centennial Campus in Raleigh, NC, and is part of the university’s College of Engineering. The instructional center opened in 2007 with a mission to contribute to the social and economic well-being of the state of North Carolina by providing a wide variety of high-quality educational and training opportunities to develop skilled professionals for the biomanufacturing industry.
This is accomplished by providing hands-on educational opportunities for undergraduate and graduate students as well as professionals in the areas of biopharmaceutical process development and manufacturing.
The center offers a number of academic degree programs for NC State undergraduate and graduate students built on an array of content including microbiology, molecular biology techniques, basic principles of fermentation, cell culture, bioseparations, upstream and downstream process development, biopharmaceutical analysis, and CGMP manufacturing operations.
Annually, about 850 NC State students are enrolled in BTEC’s academic courses, and between 300 and 400 professionals are enrolled in its short courses. This includes inspectors from the US FDA, who participate in a biomanufacturing training program delivered by BTEC.
BTEC’s professional development program offers both open-enrollment courses, which are open to the public, and customized courses, in which content is tailored to meet an organization’s needs. Like the academic programs, coursework spans a variety of content areas including biomanufacturing, bioprocess development, and analytical technologies. The professional development program has served nearly 2,000 individuals who have visited from from >200 organizations all over the world.
In addition to training and education, BTEC’s bioprocess and analytical services program supports partners from industry, academia, and government agencies. The program’s staff is capable of tackling a wide range of problems spanning process development, technology evaluation, technology development, analytical testing, and analytical method development.
The facility contains 82,500 ft2 of laboratory, classroom, and office space and is equipped with over US$15 million of industry-standard equipment. Laboratories range from bench scale to those supporting the largest simulated-CGMP pilot plant in the United States dedicated to education and training.
References
1 Ben Locwin (Biogen), private conversation.
2 Chalk S. The BioPhorum Operations Group Report 2016; https://issuu.com/karenali57/docs/biophorum_report_2016.
3 Emergent Research. Intuit 2020 Report: Twenty Trends That Will Shape the Next Decade; http://http-download.intuit.com/http.intuit/CMO/intuit/futureofsmallbusiness/intuit_2020_report.pdf.
4 Association of Talent Development. State of the Industry (2015); www.td.org/Professional-Resources/State-of-the-Industry-Report.
John Balchunas is the assistant director of professional development programs at the Biomanufacturing Training and Education Center, North Carolina State University; jebalchu@ncsu.edu.
Very nice article, totally what I needed.|