The global biopharmaceutical industry had been growing robustly even before the COVID-19 pandemic. According to the BioPlan Associates Top 1000 Biofacility Index and Biomanufacturers Database (1), bioprocessing capacity worldwide increased an average of 12% over the past decade. China has seen nearly double that rate. India’s bioprocessing segment also is showing strong growth. Because those regions represent 37% of the world’s population — and with rapidly growing middle-class economies, — demand for biologics there is outstripping that elsewhere.
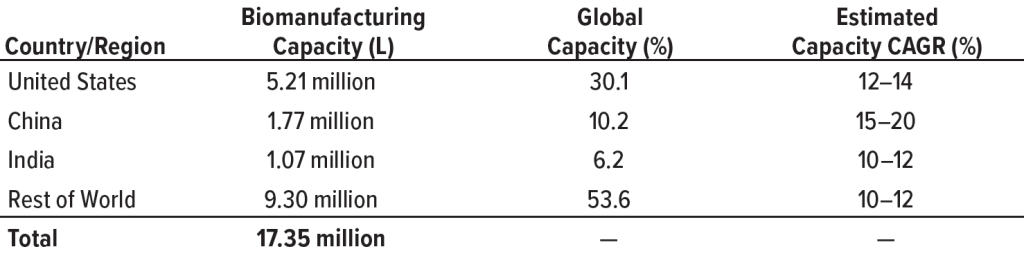
Table 1: Global comparison of biomanufacturing capacity; data from the BioPlan
Associates Top 1000 Biofacility Index and Biomanufacturers Database (CAGR =
compound annual growth rate).
Historically, Western technologies, equipment, reagents, and consumables have been used to produce biologics in China and India. Now, with COVID-19 disrupting international supply chains, domestic suppliers in those regions have begun to take on more important roles than ever before. Shortages and long lead times for imported materials and equipment have created delays, raising opportunities for local vendors that might not have come about otherwise. The resulting acceleration of local competition is likely to influence Asia’s pharmaceutical supply chains long after the COVID-19 pandemic is controlled.
Emergence of Asian Biopharmaceutical Industry
China and India are well positioned as global participants in markets for both small- and large-molecule drugs. They rank second and third, respectively, in pharmaceutical production by nation. Facilities in India account for 8–9% of global biopharmaceutical capacity. And China is home to dozens of cell and gene therapy developers, a number that is second only to the United States (2).
Several factors have contributed to the biopharmaceutical industry’s growth in those countries. Those regions dominate markets for branded generics of small-molecule drugs and raise opportunities for production of complex generics, specialty pharmaceuticals, biosimilars, and even novel biological drugs and vaccines (including COVID-19 vaccines). Low prices, inexpensive labor, and changing government policies also are contributing to overall growth. China’s biopharmaceutical industry is expanding rapidly, driven by a wave of biologics license applications (BLAs) for monoclonal antibody (MAb) products.
China and India also have growing service segments. China-based contract development and manufacturing organizations (CDMOs) account for ~25% of the country’s bioproduction capacity (3), although contract manufacturers owned by Western companies (e.g., Boehringer Ingelheim and Lonza) find their capacity somewhat limited because the Chinese government regulates CDMOs strictly. In India’s biopharmaceutical sector, large manufacturers (usually multinational vaccine producers) generate two-thirds of revenue reported (4).
The global biopharmaceutical industry emphasizes strict adherence to good manufacturing practices (GMPs), especially when developing products for export to Western markets. Thus, Indian and Chinese biomanufacturers and suppliers must enhance their capabilities to ensure GMP compliance and improve documentation for regulatory review.
Bioprocess Consumables
With millions of liters used annually, buffers are a major consumable in the biopharmaceutical industry. In India, domestic manufacturers represent ~25% of the country’s annual buffer consumption. That percentage continues to rise, and COVID-19’s impacts on supply chains are accelerating the trend.
In China, ~90% of the market is occupied by domestic players. Domestic chemical suppliers are favored except whenever a buffer is locally available. That tendency stems from a good supply chain, low prices, timely delivery, and most important, certain advantages provided through government support.
Critical Criteria
Key considerations for selecting domestic suppliers in Asia include quality, traceability, timing, and cost.
Quality of raw materials and compliance with GMP standards are important factors in the biopharmaceutical industry. Most biomanufacturers agree that imported current good manufacturing practice (CGMP)-grade buffers are of better quality than are counterparts from domestic vendors. However, at least at present, domestic suppliers are meeting demand for significant bioprocess segments.
Supply-Chain and Material Traceability: A consistent supply chain is critical. The COVID-19 pandemic has strained global supply chains, and biopharmaceutical companies in both India and China are feeling pressure to maintain inventory. Market complexities in both countries are creating additional challenges. It has become imperative to assemble a network of suppliers with good distribution practices. Traceability of material is also a significant factor.
Delivery Times: India’s supply chain depends on the location of nearby facilities. Thus, biomanufacturers usually prefer regional vendors, assuming acceptable quality. Supply-chain inconsistency could necessitate additional risk assessments, require revalidation, and incur new costs.
Cost of Reagents: Because domestic competition among chemical companies has increased, local biomanufacturing facilities will be unwilling to pay high prices for high-quality reagents. Chinese companies, in particular, tend to seek out inexpensive options in response to cost sensitivities. Government policies such as price structures for biologics sales in value-based procurement programs will exacerbate those issues in China.
Challenges to Western Suppliers
In China and India, CGMP quality is a major concern for facilities that want to export their products to Western countries; CDMOs working with Western clients; and small, Western-funded biotechnology companies. But many facilities in China today are operating only domestically and therefore can source certain raw materials from domestic suppliers more easily than they can from foreign companies. Chinese biopharmaceutical companies have yet to succeed in exporting therapeutics to Western markets. However, many “double IND” applications — e.g., for production of new investigational drugs in the United States and China, Australia and China, or Japan and China — have been approved for MAbs and insulin products from Chinese companies. It might be just a matter of time before Chinese biopharmaceutical companies sell GMP biologics in developed regions.
Major suppliers might start producing consumables locally in China and India. That could shorten lead times for raw materials and increase supply-chain stability, but it might decrease prices for products sold locally. Merck Millipore already has established a facility for bioprocess reagents in Nantong, China; Cytiva has built a facility in Guangzhou.
In India, three biopharmaceutical companies earn 46% of that industry’s total revenue. The top 20 companies represent 89% (4). Major companies such as Biocon Ltd., Serum Institute of India, Lupin Ltd., and Sun Pharmaceutical Industries Ltd. have a large export share to serve the Western market (4). They also have established GMP-compliant manufacturing facilities. Thus, 89% of the Indian industry consumes CGMP reagents.
The competitive landscape in India currently favors Western suppliers. Domestic manufacturers are not equipped to meet international standards, and they face difficulties in receiving global acceptance. Thus, demand for GMP reagents from Europe and the United States continues to grow.
In BioPlan’s 18th Annual Report and Survey of Biopharmaceutical Manufacturing Capacity and Production, we show that global supplier expansions into China nearly doubled from 37.7% in 2008 to 68.3% in 2021 (5). Essentially, over two-thirds of global suppliers now have active sales programs in China, up from only one-third just 13 years ago.
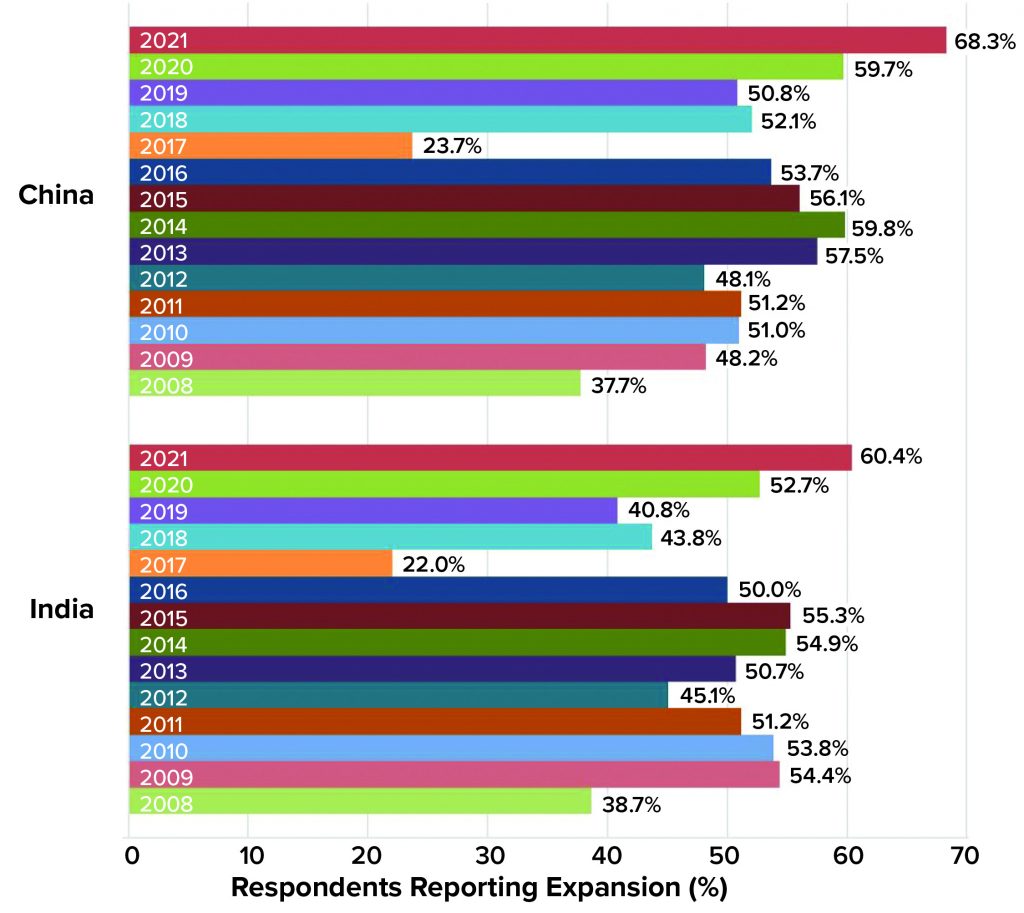
Figure 1: Percentage of BioPlan survey respondents who reported movement of global
suppliers into their respective countries, 2008–2021.
The Switch Toward Domestic Suppliers
In China, the present competitive landscape favors domestic suppliers. In India, domestic suppliers are providing affordable alternatives and have a robust supply chain but are struggling for global recognition. With the biomanufacturing industry’s focus on GMP compliance, India plans to adopt GMP practices set by the World Health Organization (WHO). In the coming years, the country also will participate in the Pharmaceutical Inspection Convention (PIC) and International Council on Harmonisation of Technical Requirements for Pharmaceuticals for Human Use (ICH) (6).
Price differences between domestic and imported reagents can be significant. That is driving demand potential, giving domestic suppliers opportunities to “up their game” to produce high-quality, GMP reagents. Essentially, Western suppliers are creating their own future competition.
The COVID-19 pandemic has paved a path forward for domestic vendors in India’s and China’s biopharmaceutical segments. During lockdowns, many multinational vendors had trouble ensuring stable supply chains. Lead times were long because many products needed to be imported. As a result, domestic biomanufacturers have added supplies from domestic vendors into their procurement platforms for trial use.
Government initiatives in those regions seek to increase the number of domestic substitutions in biopharmaceutical supply chains — and the COVID-19 pandemic has enabled domestic vendors to demonstrate the disadvantages of import-heavy supply chains. In October 2020, the 13th Standing Committee of the Chinese National People’s Congress passed the Biosecurity Act, which emphasizes that municipal governments should support research and development for key technologies and products. In May 2021, Shanghai’s municipal government announced plans to sponsor the bioprocess supply industry. Thus, domestic growth has surged in China, evidenced by single-use suppliers building new facilities in Shanghai and elsewhere.
In India, changing government policies and a focus on “Make-in-India” supplies also favor domestic biopharmaceutical players. Schemes such as the National Biopharma Mission seek to nurture an ecosystem for India’s technological and product-development capabilities. The Indian government also has outfitted incentive programs such as the Production-Linked Incentive Scheme with an outlay of US$22 billion to encourage development of products using domestically sourced raw materials (6).
After the pandemic, major players such as Biocon plan to reduce their reliance on single vendors and geographies for procurement of key materials, especially for manufacturing of active pharmaceutical ingredients (7).
Leveraging New Opportunities
China and India both have considerable biomanufacturing capabilities, but strict adherence to global GMP standards will be critical to both countries’ efforts to build confidence in their biologics’ safety and effectiveness. Such credibility is needed to sustain growth of these Asian biopharmaceutical and bioprocess-supply industries. They have already ramped up their capabilities and technologies to move toward GMP standards. Chinese and Indian suppliers are also beginning to compete effectively domestically, and it might be only a matter of time before they are competing in Western markets.
Available data depict an Asian bioprocess market that supports the growth of domestic suppliers. But because high-quality reagents are needed, domestic suppliers must modify their business models significantly to enable effective, long-term global competition. However, boosted by current events and policies, existing players have found new opportunities and have begun to make meaningful investments toward meeting global standards.
References
1 Top 1000 Biofacility Index and Biomanufacturers Database. BioPlan Associates: Rockville, MD, 2021; https://www.top1000bio.com.
2 India Bioeconomy Report. Biotechnology Industry Research Assistance Council: New Delhi, India, March 2021; https://birac.nic.in/webcontent/1615182060_Indian_BioEconomy_Report_2021.pdf.
3 Directory of Top 100 Biopharmaceutical Manufacturers in China. BioPlan Associates: Rockville, MD, 2021; https://www.bioplanassociates.com/china-top-60.
4 Indian Biopharma Industry Crosses 22,000 Crores, Grows 12%. Biospectrum 17(6) 2019; https://www.biospectrumindia.com/pdf/Top-20-Biopharma.pdf.
5 Langer ES, et al. 18th Annual Report and Survey of Biopharmaceutical Manufacturing Capacity and Production. BioPlan Associates: Rockville, MD, 2021, https://www.bioplanassociates.com/18th.
6 Indian Pharmaceutical Industry 2021: Future Is Now. Ernst & Young, February 2021; https://assets.ey.com/content/dam/ey-sites/ey-com/en_in/topics/health/2021/ey-ficci-indian-pharma-report-2021.pdf?download.
7 The Impact Manifesto: Annual Report 2020. Biocon Ltd.: Bengaluru, India, 2020; https://www.biocon.com/docs/Biocon_Annual_Report_2020.pdf.
Smita Khanna, PhD, is a biopharmaceutical-industry and healthcare market researcher/analyst as well as director of research at BioPlan Associates; 1-301-921-5979; smitakhanna@bioplanassociates.com; https://www.bioplanassociates.com.