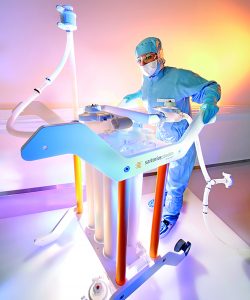
The ready-to-use MaxiCaps MR system is entirely disposable and enables the integration of three, six, or nine 30-inch filter capsules.
Whether viral vectors are clarified or the bioburden after cell harvest needs to be reduced to recover antibodies, such applications in biopharmaceutical production require large filtration areas. Single-use technologies are indispensable in many such bioprocesses. Although some single-use filter assemblies have reached their limits, Sartorius Stedim Biotech has made developments to revolutionize these production steps.
Scale-Up Limitations in Single-Use technology
Conventional stainless steel process systems have been established for decades in the pharmaceutical industry. They are the basis of safe and reliable manufacturing processes for both classical pharmaceuticals and advanced biologics. Complexity and cost efficiency in biopharmaceutical production require great flexibility. Thus, most leading biopharmaceutical manufacturers are increasingly relying on modular single-use systems designed for flexible use.
But the rapid introduction of technologies that enable such flexibility has led to a number of different components and solutions over the past years. As batch volumes produced using single-use technologies increase, the processes for such batches become more complex and involve higher risks. The challenges of a complete single-use process are inherent in the diversity and large number of parts to be connected. Particularly when scaling up batch sizes to 1,000–2,000 L, users discover limitations in some process steps and thus face significant problems.
Minimizing Risk Even in Large-Scale Filtration
In cooperation with a multinational pharmaceutical company, Sartorius Stedim Biotech faced the task of developing a single-use solution for large-volume filtration steps that would minimize risk, time, and effort. The challenge was to incorporate up to 27 m² of filter area into a single, closed, and ready-to-use device to minimize the risk of faulty connections between filter capsules and thus lessen the risk of leakage for users.
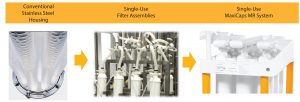
Figure 1: Stainless steel multiround housings are the established solution for conventional large-scale filtration processes. Complex filter assemblies with multiple cable-tie connections, T-pieces and complex tubing manifolds are the single-use equivalent. MaxiCaps MR combines all advantages of a single-use solution with those of a conventional system.
Standardization, Installation, Automation
The result of this collaboration was the development of MaxiCaps MR filtration system, which replaces complex filter and tubing assemblies consisting of several 30-inch capsules and sterile connections used so far. This preassembled and presterilized device enables three, six, or nine 30-inch capsules to be integrated into a single system with only one connection in a process. That saves not only time and expense, but also 90% of sterile connections, 90% of tubing, and up to 90% of integrity testing time. The system saves process time because it is ready to use, unlike conventional filtration systems. Its efficient design minimizes footprint in cleanrooms.
Moreover, simultaneous flow through the entire filter area of this closed system ensures efficient filter use, thus optimizing the filtration process. The MaxiCaps MR system is the logical next step in standardization, easy installation, and risk mitigation in single-use systems. It is completely made of plastic, with a design that systematically implements the single-use concept for large volumes. Single-use pressure and flow-rate sensors
can be connected easily to the MaxiCaps MR system. This is the first step in the direction of a fully automated system that is already being assessed by users in a production environment.
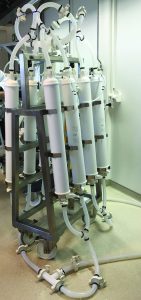
Large-scale filter assemblies today: multiple cable-tie connections, T-pieces, complex tubing manifolds
Applications
The MaxiCaps MR system provides a filter area of up to 27 m² for prefilters and sterilizing-grade filters and has a number of applications. It is tailored to accommodate large-scale filtration of media and buffers in volumes of 5,000 L and more. Contract manufacturing organizations (CMOs) that use modular single-use processes to adapt to changing products tend to prefer generously sized filtration areas for initial bioburden reduction and sterile filtration as post–cell-harvest steps for monoclonal antibodies (MAbs), for example. In this case, the system already in use has proved its efficiency downstream of 2,000-L single-use bioreactors.
For new (not perfectly defined) processes in which centrifugation is not yet qualified, higher filtration areas are needed to ensure safety and reliability. A polypropylene or glass-fiber prefilter with a nominal pore size of 1.2 µm often is used in the first post–cell-harvest clarification step for viral vaccines, such as for human cytomegalovirus (CMV) in the range of 150–200 nm. In such processes, the closed, completely single-use, and ready-to-go MaxiCaps MR system is a significant improvement over traditional filters and already being used for batch sizes of 250 L and higher.
For most applications, the major focus is on total throughput and less so on flow
rate. The MaxiCaps MR system minimizes risk, time, and effort for applications in which filters tend to become readily blocked, requiring a large filtration area.
System Details
The large-scale single-use MaxiCaps MR filtration system is based on 30-inch MaxiCaps filter capsules. Filters and materials have been established for decades and are already in use in today’s single-use filter-and-tubing assemblies. The abbreviation “MR†stands for “multiround†and is intended to be associated with conventional multiround housing configurations used in classical stainless steel processes. Filter solutions for large filtration areas evolved from large stainless steel MR systems to complex single-use constructions to the MaxiCaps MR system, which offers all the advantages but none of the disadvantages of a single-use solution. The gamma-irradiated system is presterilized, preassembled, and doublepackaged, so it minimizes time and effort for installation.
Minimum Use of Tubing Maximized Flexibility |
Inlet/Outlet: One set of tubing with three connection options (sterile connector, Tri- Clamp connector, or weldable thermoplastic elastomer (TPE) tubing) |
Central Sterile Venting: A short length of tube with a sight glass for checking the water level during flushing of the filters; the new Sartopore Air filter with a hydrophobic polyether sulfone (PES) membrane has been specially designed for single-use applications and ensures both sterile air filtration and venting of the MaxiCaps MR system. |
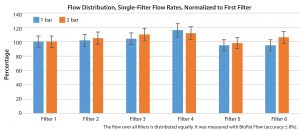
Figure 2: Simultaneous flow through a multicapsule assembly is decisive when it comes to efficient use of filtration area. The central distribution pipe ensures optimal flow through all filter capsules. This flow also has been validated.
The new system is configurable based on standard options. Users can choose three, six, or nine filter capsules. Either prefilters or sterile filters of different types can be used in one system. Therefore, the filtration area can be between 4 m² and 27 m². Three capsules each are held adjacent to one another by a plastic holder, ensuring simultaneous flow through all filter elements (Figure 2). Halogen-free materials are used exclusively, eliminating the drawbacks of fluorinated or chlorinated compounds that occasionally result in high extractables and require more complicated disposal. Regardless of the number of filters in the MaxiCaps MR system, there is only one inlet and one outlet and only one air filter for central sterile venting. Single-use valves on those three ports ensure optimal control of various steps such as flushing, venting, filtration, and integrity testing. Likewise, tubing is used only at those three points for the inlet, outlet, and sterile venting.
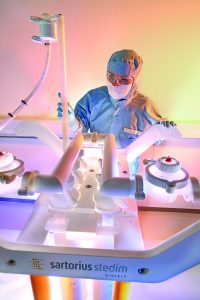
Central sterile venting using the Sartopore Air filter allows a completely closed single-use system design.
Only two tube connections need to be made to integrate the system into a user’s process, thereby minimizing the risk of a handling error or leakage. The system has undergone comprehensive validation testing, and its packaging for transportation meets ASTM D4169-09 requirements. Waste disposal also has been taken into account. Although the system appears to be complex at first glance, a minimum amount of polypropylene material has been used, which facilitates disassembly and disposal.
The central sterilizing-grade air filter (Sartopore Air) ensures simple, sterile venting of the completely contained system. If an integrity testing system (such as Sartocheck) is connected to the MaxiCaps MR system, integrity can be verified by running only one test (as opposed to the need for individual testing required for individual capsules). So the system reduces the time needed for integrity testing by up to four hours.
 Showcase of Facts |
 How the MaxiCaps MR system differs from current single-use filter solutions:
|
A New Dimension
The MaxiCaps MR system is the first single-use equivalent to large-scale, multiround filter configurations provided by stainless steel systems. It combines all the advantages of a single-use solution with those of a conventional system, without increasing the time and effort of installation or the risk of user error during scale-up. Its innovative design meets the requirements of today’s challenging pharmaceutical environment and the need for simple and safe single-use solutions for large-volume production.
Corresponding author Nikolai von Knauer is product manager of Single-Use Filtration Solutions; nikolai.vonknauer@sartorius-stedim.com; 49-551-308-2473. Dr. Thomas Loewe is director of R&D Filtration Devices, and Dr. Jens Meyer is marketing manager of Filtration Technologies at Sartorius Stedim Biotech GmbH, Goettingen, Germany.
Sartopore and MaxiCaps are trademarks of Sartorius Stedim Biotech.