Over the past year, most of China’s biomanufacturing facilities have been engaged in active facility expansion. Based on our research of facilities under active construction, that growth has expanded total capacity in China by over 10%. Our research updates the Top 60 Biopharmaceutical Manufacturers in China directory from BioPlan Associates (1) and shows a continuing increase in new bioprocess capacity. This trend is unlikely to abate. As well as contacting our top 60 biomanufacturers, in fact, we contacted a number of smaller companies and industry observers. The resulting data show that a majority of Chinese companies — including makers of therapeutic monoclonal antibodies (MAbs), recombinant insulins, and vaccines, as well as contract manufacturers of biologics — expanded/upgraded their facilities in 2017.
For example, Shanghai Henglius Biotech (a leader in MAb development in China) expanded its bioreactor capacity by four 2,000-L units in 2017. The same company just signed an agreement with local authorities to develop a new construction site in Shanghai. And 3SBio (a major maker of epoetin and thrombopoietin in China) signed a contract to buy the contract development and manufacturing (CDMO) unit of Canada’s Therapure Biopharma Inc. for US$290 million in September 2017. That investment is intended to help 3SBio enter the North America market. Also last year, WuXi Biologics (the biggest contract manufacturer of biologics in China) completed its own current good manufacturing practice (CGMP) biologics manufacturing facility in Wuxi city and started full operations with 30,000 L of bioreactor capacity.
We believe that this overall industry growth is likely to continue in China. Our study shows that nearly 40,000 L in manufacturing capacity for biologics is under construction there. And we expect that increased capacity to be in operation within two to three years (1).
Key Factors Driving the Capacity Increase
Several drivers are behind the significant increase in bioprocessing capacity. The most important of these is pipeline development of biosimilar/biobetter therapeutic MAbs by Chinese companies. This country is a latecomer in the development of MAb therapeutics. Historically, most domestic biological manufacturers have been engaged in production of insulin, vaccines, growth hormones, interleukins, blood factors, and interferons. Most of those companies have been using bacterial-based expression systems. But recent years have witnessed significant investment and robust growth in the MAb subsector in China, with mammalian-cell–based expression systems now proliferating. Successful launch of several biosimilar versions of MAb therapeutics by domestic companies (e.g., Kanghong Pharma’s Langmu vascular endothelial growth factor A inhibitor for macular degeneration) has assured many biotechnology industry insiders that Chinese companies can compete effectively with their multinational company (MNC) peers. Until now, this segment in China has been dominated by those companies.
With strong support from their government, many Chinese companies have entered the biopharmaceutical sector. Along with the giants of chemical small-molecule drugs, some recently founded companies are focusing on developing MAb therapeutics. BioPlan Associates research has shown that among the top 60 biomanufacturers in China, more than half have therapeutic MAb pipeline products in clinical development or ready for investigational new drug (IND) applications. Except for a few established MAb makers, most of those companies have not yet launched a MAb therapeutic and have operated at pilot-scale manufacturing for biologics, at best. Thus, as their MAb pipelines reach clinical stage, they will need to start planning new commercial production facilities or otherwise rely on external partners for contract manufacturing.
Regulatory Changes: We also see marketing authorization holder (MAH) system reforms that have opened the door for contract manufacturing of biologics in China. This is a key factor driving capacity growth. Previously, Chinese drug companies had to develop their own production lines and were not allowed to resort to contract manufacturing organizations (CMOs), so innovators in China relied almost entirely on overseas manufacturers. But in 2015, the Chinese government authorized its State Council to carry out its MAH program, providing a policy breakthrough and legal basis for biopharmaceutical CMOs to operate locally.
Under the MAH system, a drug-approval number holder (whether a drug-production enterprise, a research institute, or a single researcher) is required to market the approved drugs individually and take responsibility for them throughout their entire life cycles. After receiving their approval numbers, holders are allowed to manufacture on their own or choose contract manufacturers. Our company’s most recent analysis in 2018 revealed rapid growth of contract biomanufacturers in China as new companies are getting founded and existing ones expand their facilities. For example, full-service CDMO C-Mab was founded in 2017 and just completed its facility at the end of the year. Just Therapeutics — an integrated design company that provides services in molecular design, process development, and product manufacturing — is constructing a single-use facility with 2,000-L bioreactors. The more established contract research/manufacturing companies (e.g., WuXi Biologics and Shang Pharma) recently built or expansded their biologics manufacturing facilities under construction now. It is noteworthy that most of China’s contract manufacturing facilities are located in the Yangtze delta region, probably because that area boasts a significant amount of biologics development activity and a high concentration of industry veterans with overseas experience.
The vaccine sector also is enjoying healthy growth here as everywhere. That may be due to optimistic projections of demand after China’s rule change to permit second-child family planning. Also, the country has better prospects for exporting domestic products as its vaccine makers get World Health Organization (WHO) prequalification. In addition, with the development of new vaccines — e.g., for influenza, human papilloma virus (HPV), EV71, rabies, and rotavirus) — by domestic companies, the need for capacity is growing. Those new vaccines are class 2 vaccines, which means they are paid for by individuals; class 1 vaccines are given free of charge by the government. Although MNCs used to dominate this subsector in China, domestic vaccine makers lured by higher profit margins for paid vaccines are looking for expansion opportunities. Among the 10 vaccine makers listed in our top-60 directory, six are currently expanding their manufacturing capacities, and three just have completed upgrades/expansion of facilities within the past two years. The increased capacity is concentrated on making class 2 vaccines.
Single-Use Facilities on the Rise
Another global trend worthy of note in China is the introduction of single-use technologies (SUTs) for bioprocessing. Despite their higher costs compared with stainless steel systems, SU devices are increasingly popular for new facilities. Our company has projected that with a dearth of legacy stainless-steel equipment in place already, China is relatively open for single-use systems. In fact, given the much lower capital costs for facility build-outs that come with using SU equipment, such strategies make good sense in this country, where cost sensitivities continue to be high. SUT strategies thus work well in China, especially for new biotechnology companies that are focusing on development of MAb therapeutics and for which more money is available to invest in research and development (R&D) and innovation than in later stage bioprocessing facility build-outs. Contract biomanufacturing companies, especially those with Western backgrounds, also are looking closely at SU bioprocessing systems. Relatively young companies that are engaged in MAb development — including Henglius Biopharma, Innovent Bio, Akeso Biopharma, and BeiGene — in particular rely on SU equipment, partly to lessen their necessary capital expenditures. Meanwhile, contract manufacturers currently have the biggest capacity of single-use facilities. For example, consider the following:
- The new WuXi Biologics facility that started operation in 2017 is the largest biomanufacturing facility using single-use bioreactors in the world.
- The Wuhan-based contract manufacturer JHL Biotech, which recently implemented a KUBio modular factory from GE Healthcare, also has single-use manufacturing capacity of 10,000 L since 2016.
- Pfizer is currently building a commercial manufacturing facility based on SUTs in Hangzhou for biosimilar drugs.
At the same time, however, we see a relative reluctance among large domestic pharmaceutical companies to rely solely on single-use solutions, even in their new facilities for biologics. Interviews with decision makers in such companies usually indicate that price is the major concern — once again illustrating China’s price-sensitive business culture.
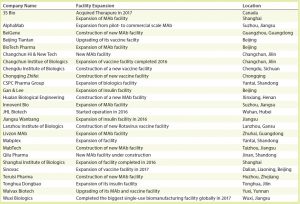
Table 1: Select Chinese biomanufacturers with expansion plans or facility expansions completed within the past two years
Further Growth or Overcapacity?
As a late comer in the global biopharmaceutical industry, China has been playing catch-up in bioprocessing capacity over the past decade. We project that the increase in biomanufacturing capacity there will continue over the near term, but our research clearly shows that major commercial-scale manufacturing facilities are currently under construction. Further, news is announced regularly of biosimilar/biobetter versions of MAb therapeutics entering clinical development from companies without commercial-scale capacities. Those biosimilars developers either will build commercial facilities of their own or (more likely) use CMOs.
In either situation, domestic capacity demands will continue to be generated. We also expect domestic Chinese vaccine makers to continue their efforts to develop new class 2 vaccines, which in turn will generate demand for capacity.
Legitimate concerns arise here that overcapacity could become an issue in the long run, as we have witnessed in China’s manufacturing of steel, textiles, and household electronics, as well as coal refining and other industry segments. We also need to consider that unlike many other manufacturing sectors in China, most biomanufacturing capacity in China will be used to meet the demands from domestic markets rather than for export. That will continue to be the case until made-in-China biologics break through to receive market approvals from the US Food and Drug Administration (FDA) and European Medicines Agency (EMA).
Note that the Chinese government and investment community have been very supportive in providing support for domestic Chinese biologics companies and the country’s biotechnology industry in general. However, that could cause misalignment in the level of incentives and investments for pipeline products and facilities. Meanwhile, China’s own food and drug administration (CFDA) announced wide-ranging reform plans in 2017 that are being interpreted as largely intended to speed up the entry of innovative drugs from MNC drug products into China. That could have negative consequences for the prospects of made-in-China biosimilars.
We also see warning signs of overdraft in China’s national healthcare insurance system. Further, as the country’s economy begins to cool, the buying power of Chinese patients may not grow as quickly as it did in the past decade, which could slow domestic demand for biologics. On the other hand, as the quality of China’s biologics improves and local production meets GMP standards, global opportunities will arise for the best and most efficient Chinese biologics makers. Calculating the many factors driving the build-up of China’s biologics capacity continues to be challenging in this very dynamic business environment.
Reference
1 Top 60 Biopharmaceutical Facilities in China (database). BioPlan Associates, Inc.: Rockville, MD, March 2017; www.bioplanassociates.com (updated February 2018).
Vicky Qing Xia is project director, and Leo Cai Yang is a project manager at BioPlan Associates, Inc., 1-301-921-5979; www.bioplanassociates.com.