Regenxbio says increasing competition for capacity in the CMO space prompted the adoption of a hybrid gene therapy manufacturing strategy.
Industry demand for contract manufacturing organizations (CMOs) with the technical skills required to manufacture gene therapies has increased in recent years.
According to the Alliance for Regenerative Medicine, as of Q3 last year, 370 trials involving gene therapies were ongoing, which is an increase on the 351 underway in the equivalent period in 2018.
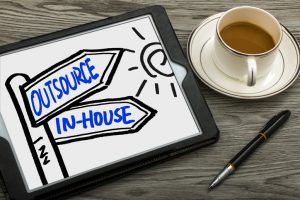
Image: iStock/cacaroot
Katie Masterson, director of manufacturing operations at Regenxbio, told the audience at the BPI US virtual conference finding gene therapy contractors has become more difficult.
“CMO network availability today is constrained…for gene therapy it is limited as the industry is experiencing constraints because of the growing demand for these products as clinical trials and INDs have increased over the years.â€
The COVID-19 pandemic has exacerbated the issue Masterson said, explaining many contractors are now prioritizing capacity for SARS-CoV-2 vaccine development and production.
This view is supported by WHO data which show there are 38 vaccines for SAR-CoV-2 in clinical development and a further 149 in preclinical trials.
Inhouse and outsource
In response, Regenxbio plans to use both inhouse capacity and a network of CMOs to manufacture its gene therapies.
Masterson said, “The organization decided that our strategy would consist of a combination of CMO capacity as well as the establishment of an internal manufacturing capability for both BDS [bulk drug substance] and FDP [finished drug product].â€
The firm’s CMO network includes Fujifilm Diosynth Biotechnologies, under a strategic partnership established in 2018, and Advanced Bioscience Labs, which it teamed up with in 2016.
Plans for Regenxbio’s in-house capacity were unveiled in 2019 when the firm said it would set up a GMP grade vector production facility at its Rockville, Maryland headquarters.
According to Masterson “The new corporate, research and manufacturing headquarters will be ready in late 2021 with cGMP operations ready to perform early engineering runs at scales above 1,000 L in 2022.
She cited the housing of production capacity and quality control functions in the same space as a major advantage, explaining “It really will be 100% in our control, compared to the CMO only model.â€