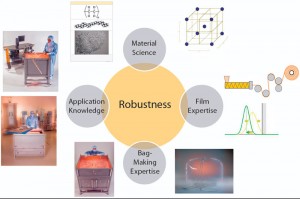
Figure 1: Film and bag development based on a quality by design (QbD) approach, with expertise in material science, application know-how, film, weld, and bag making
With the increased use of disposable bioprocessing bags in all critical process steps of the biopharmaceutical drug production, there is a growing requirement for high-quality, robust, and easy-to-handle bioprocessing bags. The new generation of films and bags must combine multiple mechanical, physical, and chemical properties to make these products suitable and scalable for all processing steps in upstream, downstream, and final filling operations, including cell culture in rocking motion and/or stirred-tank, single-use bioreactors as well as storage, mixing, shipping, and freezing.
In partnership with our resin and film suppliers, Sartorius Stedim Biotech’s polymer and film experts have selected the best raw materials, optimized the design space of the extrusion process, and defined the critical welding parameters following the principles of quality by design (QbD). With this approach, we have developed a new polyethylene film and new bags that combine strength and flexibility, the two prerequisites that will provide for robust and convenient single-use bioprocessing.
The robustness of our new S80 polyethylene film structure (used in manufacturing new Flexsafe bags) has been demonstrated by means of standard flex-durability, tensile strength, elongation, and energy at break testing. Furthermore, we applied a water-burst test developed in house using model bags and worst-case application testing of two-dimensional (2-D) rocking-motion cell culture bags and three-dimensional (3-D) stirred bioreactor bags to confirm the robustness of new Flexsafe bags in different applications. Notably, our new Flexsafe 3-D shipping bags passed the most stringent ASTM D4169 test for air and truck shipment.
The thickness, strength, and flexibility of S80 film improve its mechanical robustness and make it suitable for all bioprocessing applications. Its strength significantly reduces the risk of accidental damage to bags due to inappropriate handling. And the flexibility enables convenient installation and self-deployment of each bag in its container.
Industry Demands
The need for product quality, robustness, and integrity has been ranked in a number of surveys as the primary bioindustry requirement (1). Because single-use bags offer multiple technical and economic benefits, they are broadly adopted throughout the biopharmaceutical drug industry to help companies achieve rapid and flexible development and commercial production of monoclonal antibodies (MAbs), other recombinant proteins, and vaccines. The biotechnology industry is now expanding its implementation of single-use bags into all bioprocess steps for applications such as cell culture, storage, shipping, mixing, freeze and thaw, and final filling (2).
With that growing implementation of single-use bags, requirements are increasing for outstanding product quality, assurance of supply, change control, robustness, ease of use, and scalability. These are important throughout all applications of single-use bioprocessing, from cell culture to shipping of bulk drug substances and final filling of drug products.
Partnerships with Resin and Film Suppliers
Developing innovative film and bioprocessing bags that meet all those emerging demands requires different disciplines and skills and expertise. So the new S80 multilayer polyethylene (PE) film from Sartorius Stedim Biotech has been specified and designed in partnership with Südpack, a leading film manufacturer, and in close collaboration with polymer and additive suppliers. This collaboration combines material science, application know-how, film-extrusion knowledge, and welding and bag-making expertise.
The resins in each layer of the S80 film and their associated extrusion parameters were selected after extensive prototyping in which various polymers and film compositions were evaluated to achieve the best mechanical properties. Our main objective was to obtain the highest film robustness: an optimal combination of strength and flexibility with the most reliable and robust welds. That in turn enabled us to design completely new bioprocessing Flexsafe bags suitable and scalable for all bioprocessing steps in upstream, downstream, and final filling. Flexsafe bags meet user-requirement specifications (URS) of both rocking motion and stirred-tank single-use bioreactor applications as well as medium, buffer, and intermediate storage; shipping, mixing, and freezing; and aseptic filling of bulk drug products.
Development of this innovative Flexsafe bioprocessing bag range followed a QbD approach to achieve reliable and robust bioprocessing bags suitable for all applications. This approach included selection of appropriate resins and additives and subsequent establishment of specifications and controls, definition of the film-extrusion process design space, and validation and control of the welding and overall bag-making process.
Quality by Design Approach
As described in ICH guidelines Q8, Q9, and Q10 and applied to new product development, a QbD approach ensures that developed products consistently meet intended performance criteria (3–6). Well-established and open supplier relationships and knowledge sharing are critical for selecting appropriate raw materials, identifying relevant specifications, and establishing necessary controls to achieve consistent robustness of the final single-use bag.
Our QbD approach to achieving consistent robustness for Flexsafe bags started with an in-depth understanding of the intended application and definition of the URS (Figure 2). Today, nearly all unit operations in biopharmaceutical drug development and production can be performed using single-use solutions. However, the required mechanical and physical properties can vary greatly by application. For example, a bag used in rocking-motion cell culture or in liquid shipping applications requires a very flexible film that resists material fatigue. A bag used in large-scale mixing applications or in a stirred-tank bioreactor design must absorb the significant hydrostatic pressure of 2,000–3,000 L of fluid. In such an application, film and weld strengths are more critical.
Further to bag robustness, routine use in production facilities calls for easy, convenient, and straightforward installation and robust handling tolerance. Here, film flexibility and easy bag deployment during installation and filling are the main targets.
The critical quality attributes (CQAs) we identified for providing robustness and ease of use in all bioprocessing applications were strength, flexibility, and weldability of polymer film. Strength significantly reduces the risk of accidental bag damage from inappropriate handling. Flexibility enables easy handling and installation and bag self-deployment in containers.
Material Science and Film Expertise
The superior robustness of single-use Flexsafe bags resulted from combining different competencies and capabilities to develop a completely new film that covers all aspects of their creation: from the choice of raw materials to final manufacturing of bioprocessing bags. Development of S80 PE film started with translating target application needs into URS, then into functional specifications for the bag, the film, and the resin and additive package.
Deep understanding of the underlying material science and expertise in polymers is required to select the right plastic resin materials and additives that will provide the desired quality attributes. As a first step, based on theoretical considerations grounded in material
expertise, robustness is designed into the polymer by those who know the plastic materials and how they behave when brought together in a multilayer film. Our polymer experts tested and selected the plastic materials that confer the best film properties: strength, flexibility, weldability, biocompatibility, purity, gas-barrier properties, and relationship with drug stability. This material selection — the number and arrangement of plastic layers and their thickness together with the extrusion approach of the multilayer film — ultimately determined the properties and overall performance of the final multilayer film structure.
In-depth knowledge of film behavior helped us choose the right plastic material mix, considering that some of those necessary properties could be antagonistic. For example, a strong and stiff film is highly resistant to impact and puncture but shows less flexibility and resistance to fatigue. A too-flexible film will not withstand hydrostatic liquid pressure in large-scale bags. Our film experts designed several film formulations and combinations and thoroughly tested them against predefined CQAs. For the S80 film, the main CQAs for characterizing our robustness target are tensile strength, elongation at break, and energy at break (5).
Film expertise is critical for development of robust single-use bioprocessing bag solutions. Robustness comes from multiple properties such as film strength, film flexibility, seal-strength resistance, film weldability, and material puncture or tear resistance. So we characterized S80 film with regard to its tensile strength, elongation at break, energy at break, and so on compared with films used for other single-use bioprocessing bags on the market.
Expressed in Newtons (N), tensile strength describes the force required to break a film. Tensile-strength data are expressed in machine direction and transversal direction to take into consideration the manufacturing process influence. This specifically characterizes the film strength required for large-volume bags to resist hydrostatic pressure. When compared with other PE films, S80 film structure shows the best strength (Figure 3).
Expressed in percentage form, elongation at break is the maximum elongation that a film can withstand before breaking. These data represent the behavior of a film with regard to deformation and resistance to breakage. A high value for elongation at break characterizes a highly flexible film that resists to material fatigue. High resistance to material fatigue is required, for example, by bags used in shipping applications or in rocking-motion cell culture applications involving movement of liquid. Compared with other PE films, S80 film structure shows the highest value of elongation at break (Figure 4).
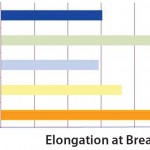
Figure 4: Elongation at break data of S80 compared with other PE films; elongation at break is shown in % of initial length of a film sample at the start of the experiment.
Expressed in Joules (J), the energy at break is the total energy required to break a film. This combines the maximum strength and maximum flexibility of the film in one direct measurement. It can be modeled by integrating the area under a strength/ elongation curve to characterize the general robustness of a film. Compared with other PE films, S80 film structure shows the best energy at break (Figure 5).
Experiment: Once the best film structure has been identified, film-extrusion expertise is also critical to ensuring lot-to-lot consistency of CQAs and reproducible robustness of a film. This is achieved by identifying and controlling the critical process parameters (CPPs) of the extrusion process. During development of the extrusion process, the team explored process variability in a multivariate design of experiment (DoE). As a criteria for robustness, the ultimate tensile strength of prototype films was measured and shown to be consistent throughout an investigated range of parameters evaluated in the DoE (Figure 6). As for cell growth, we were able to define a design space for the extrusion process that provides assurance of achieving reproducibly the desired robustness for our S80 film.
The DoE allows for creation of a model to predict results depending on the CPP settings. The contour plot shows the ultimate tensile strength in machine direction (MD), when the chill-roll parameter is kept constant but output and extrusion temperatures vary within a given range. The contour plot illustrates the design space in which the predefined specification is achieved.
As a result of our QbD approach, S80 film used in Flexsafe bags is composed of a PE contact layer and a coextruded PE-EVOH-PE backbone structure (Figure 7). The combined strength and flexibility of each layer with a total thickness of 400 μm provides extraordinary overall robustness. The resin-additive formulations for both the contact layer and backbone are completely known and controlled according to specifications. Furthermore, the extrusion process parameters are controlled within established ranges. This ensures long-term lot-to-lot consistency for all targeted critical mechanical quality attributes of Flexsafe bags — specifically, strength, flexibility, and (hence) robustness.
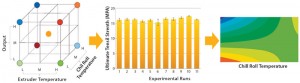
Figure 6: Example of a DoE experiment (using MODDE software) on film-extrusion design space with the ultimate tensile strength as a criterion
Welding and Bag-Making Expertise
The third critical expertise required for achieving robustness of Flexsafe single-use bioprocessing bags is in welding, sealing, and bag-making. The challenge is to define appropriate CPPs for consistently achieving the defined CQAs with a robust process. Our bag-making experts have optimized the welding, sealing, and bag manufacturing process and qualified these parameters based on a process risk analysis. Bringing together the knowledge of welding experts, application scientists, and production engineers ensures an adequate level of process understanding of the bag assembly and welding process.
CPPs for bag welding and sealing such as temperature and time have been considered in our QbD approach. Operating ranges of the welding parameters have been tested and are routinely controlled to ensure process consistency. To confirm robustness, especially of critical welds, we have established a water-burst test in which model bags are filled with water in a controlled manner. Thus, when evaluating sample bags, we found that typically our bags break at a certain overfilling level at the film rather than the welds (Figure 8).
Proven Robustness
The performance robustness of Flexsafe bags in different bioprocess steps in biopharmaceutical manufacturing has been confirmed against stringent applications such as cell culture, liquid shipping, long-term storage, and freezing applications. Robustness trials were conducted to test the performance of the product at its limit. As part of our film development, extensive robustness trials were performed under worst-case application conditions with rocking-motion bioreactor bags (100-L working volume) and stirred bioreactor bags (2,000-L working volume). Typically, these bags were filled with water to maximum their working volume. The bags were either rocked at maximum rocking rate or stirred at maximum stirrer rate for 21 days at 40 °C and maximum operating pressure. Weber et al. further explain this approach elsewhere in this special issue (7).
In addition, Flexsafe bags were tested for their robustness in air and truck shipping applications by applying the very stringent ASTM D4169-09 guideline for shipping applications (6). The testing sequence is designed to reflect worst-case conditions for air or truck shipment and performed at several temperatures. In addition to the handling test, the bags’ truck-transport behavior is tested through investigating horizontal impact (Figure 9a) or rotational shocks. Air-shipping behavior is tested by exposing a shipper to vibrations (Figure 9b), compression, or a low-pressurized environment.
Our new Flexsafe bags successfully passed the most stringent ASTM D4169 test for air and truck shipment (Figure 9).
Conclusion
With the increased implementation of single-use bags in biopharmaceutical drug production, there is a growing requirement for robust and easy-to-handle bioprocessing bags that will be suitable and scalable for all processing steps in upstream, downstream, and final-filling operations.
In partnership with our resin and film suppliers, we combined material science and film and bag-making expertise, applying the principles of QbD to select the best raw materials, optimize the design space of the extrusion process, and define the critical welding and overall bag making parameters. With this approach, our film experts designed several film formulations and combinations and were able to achieve a new 400-μm thick film structure composed of a PE contact layer and a coextruded PE-EVOH-PE backbone that combine strength and flexibility. This optimal combination makes our new S80 film the most robust and suitable for all bioprocessing applications. The strength significantly reduces the risk of bag damage due to inappropriate handling, and the flexibility provides ease of installation and self-deployment of bags in their containers.
The formulation of resins and additives are completely known and controlled by specifications, and the extrusion process and welding parameters (e.g., temperature and time) are controlled within established process parameter ranges. This ensures long-term lot-to-lot consistency of strength, flexibility, and (hence) robustness of Flexsafe bags.
The superior robustness of Flexsafe bags was first demonstrated using standard flex durability, tensile strength, elongation, and energy-at-break testing. The S80 film structure shows the best strength, the highest value of elongation at break, and the best energy at break when compared with other PE films.
Mechanical property requirements largely vary by application. Rocking motion in cell culture or liquid-shipping applications requires a very flexible film that will resist material fatigue, whereas large-scale mixing applications with significant hydrostatic pressure call for strength in both film and welds.
That is why we have also applied a water-burst test developed in house and worst-case application testing of rocking-motion cell culture and stirred bioreactor bags. We confirmed the extraordinary robustness of Flexsafe bags in various applications and at maximum operating pressure, working volume, and rocking or stirrer rate over 21 days at 40 °C.
Finally, Flexsafe bags have been tested for robustness in shipping by both air and truck, applying the very stringent ASTM D4169-09 guideline (designed to reflect worst-case conditions for air or truck shipment) at several temperatures.
Acknowledgments
Thanks to Sartorius Stedim R&D teams in Aubagne, France and Göttingen, Germany.
References
1 Langer E. Ninth Annual Report and Survey of Biopharmaceutical Capacity and Production. BioPlan Associates, Inc.: Rockville, MD, 2012; www.bioplanassociates.com/images/9th_ Annual_2012_ReportTable_of_Contents.pdf.
2 Large P. MCC Fujifilm Billingham. Single-Use Workshop, 19 September 2013. Parenteral Drug Association UK Chapter: Uxbridge, UK, www.pda.org/Chapters/ Europe/United-Kingdom.aspx.
3 ICH Q8(R2). Harmonized Tripartite Guideline: Pharmaceutical Development. US Fed. Reg. 71(98) 2009; www.ich.org/fileadmin/ Public_Web_Site/ICH_Products/Guidelines/ Quality/Q8_R1/Step4/Q8_R2_Guideline.pdf.
4 ICH Q9. Harmonized Tripartite Guideline: Quality Risk Management. US Fed. Reg. 71(106) 2006: 32105–32106; www.ich.org/ fileadmin/Public_Web_Site/ICH_Products/ Guidelines/Quality/Q9/Step4/Q9_Guideline.pdf.
5 ICH Q10: Pharmaceutical Quality System. US Fed. Reg. 74(66)2009: 15990– 15991; www.ich.org/fileadmin/Public_Web_ Site/ICH_Products/Guidelines/Quality/Q10/ Step4/Q10_Guideline.pdf.
6 Gerighausen S, Barbaroux M, Hackel H. An Approach to Quality and Security of Supply for Single-Use Bioreactors. Advances in Biochemical Engineering/Biotechnology, Volume 138. Springer- Verlag: Berlin, Germany, January 2014.
7 ASTM D882/ISO 527-3. Standard Test Method for Tensile Properties of Thin Plastic Sheeting. ASTM International: West Conshohocken, PA, 2012.
8 ASTM D4169. Standard Practice for Performance Testing of Shipping Containers and Systems. ASTM International: West Conshohocken, PA, 2009.
9 Weber A, et al. Development and Qualification of a Scalable, Disposable Bioreactor for GMP-Compliant Cell Culture. BioProcess Int. 12(8) 2014: S47–S52. c
Elisabeth Vachette is Flexel and Flexsafe product manager at Sartorius Stedim Biotech France (elisabeth.vachette@sartorius-stedim. com). Christel Fenge is vice president of marketing for fermentation technologies at Sartorius Steidm Biotech Germany. Jean- Marc Cappia is vice president of marketing for fluid management technologies at Sartorius Stedim Biotech France (jean-marc.cappia@sartorius-stedim.com). Lucie Delaunay is R&D project leader at Sartorius Stedim Biotech France. Gerhard Greller is R&D director of upstream technology at Sartorius Stedim Biotech Germany. Magali Barbaroux is R&D director at Sartorius Stedim Biotech France.