The concept of sustainability has evolved over the past few decades to describe conditions for harmonious coexistence of industry and nature while meeting socioeconomic requirements of present and future generations. For this environmentally focused report, I like the simple definition offered by Armstrong International, a provider of steam, air, and hot water systems that improve utility performance, lower energy consumption, and reduce environmental emissions. According to a brochure that in part describes its work with Pfizer, Armstrong defines this concept as “meeting the needs of current generations without compromising the needs of future generations.â€
In theory, that may imply an “either–or†situation: That is, either a facility/process is sustainable, or it isn’t. (And you could argue, then, that nothing truly is.) But in practice, moving from an unsustainable past toward a sustainable future in business is more of a continuum as companies take steps toward more environmental responsibility over time. Many are beginning to understand that considering the environment doesn’t have to add cost; it can improve efficiencies as well as public perceptions by decreasing use of materials and reducing negative environmental impacts, ultimately increasing shareholder value over the long term. Relatively sustainable development can be accomplished by understanding the flow and costs (more than simply financial) of all process inputs and outputs, building systems that can adapt to changing needs, anticipating and managing variability and risk, all while earning a profit.
Biopharmaceutical manufacturing is no stranger to regulatory concerns. All facilities must at least go through the motions of basic environmental assessment to meet EPA and local requirements. But 21st-century business is placing increased emphasis on sustainability, due not only to public pressure, but also a world of decreasing resources. This special report considers how the bioprocessing industry is beginning to incorporate related ideas into its processes and facilities. What degree of sustainability is realistic to strive for? What hidden costs of not modernizing do companies tend to miss in their evaluations, and what are the real economic advantages of going green? How are companies comparing “apples to oranges†costs of, for example, water for injection (WFI) production and clean/steam-in-place operations with those incurred in securing an uninterrupted source of disposable materials? Where are the tradeoffs specific to various methods of disposal, and how are they to be evaluated? And what lessons can the US biotech industry learn from attention paid to this topic by many European companies and regulatory agencies?
FW Biokinetics (www.fwc.com) is an engineering and design firm providing construction and validation of biopharmaceutical and vaccine facilities worldwide. The company lists environmental sustainability as one of six major trends in the industry today — alongside outsourcing growth, financial pressures, regulatory pressures, mergers and acquisitions — so it offers guidance in this area as one of its services.
“Green is here to stay,†states the corporate website. “But so much of sustainable design is simple engineering attention to detail, things we already know: saving energy, utilities optimization, water temperature, air handling, process automation strategies.†FW reports that one of its major pharmaceutical clients wants to become a leader in sustainability over the next couple years and expects the effort to cost an additional 2–3%. But the long-term benefits will dwarf that investment.
What Vendors are Doing
Early in the ongoing single-use revolution, companies offering disposable equipment and components were faced with the inevitable question: Isn’t this simply going to increase the amount of plastic waste going to our landfills (1)? Many of us — myself included — who followed the industry’s continuing foray into single-use technology raise environmental concerns the moment we hear the word disposable. Perhaps that’s one reason the Bio Process Systems Alliance, BPSA, has made efforts to nudge us all away from the term. And perhaps it has something to do with the very public efforts makers and sellers of such products are putting into sustainability research and initiatives.
Going Solar: For example, NewAge Industries is a manufacturer and fabricator of polymer tubing. Its AdvantaPure brand is familiar to many people in the bioprocess industry. The company recently completed installation at its headquarters of a 1-MW rooftop solar panel system, the sixth largest in Pennsylvania. Since going online in June 2011, the system is supplying half the company’s energy needs.
“To see what you’ve done here is quite phenomenal,†said US Representative Mike Fitzpatrick at the ribbon-cutting ceremony. “You’re demonstrating an example a lot of other manufacturing organizations should take a look at.â€
The solar project was financed in part by a US$1 million solar energy program grant from Pennsylvania’s Department of Community and Economic Development. Federal grant dollars of ∼$1.2 million were received the following month, and the total project cost was $4.2 million.
“We’ve taken a number of green steps over the past several years,†said CEO Ken Baker, “but the solar energy project was definitely the most ambitious. It’s a great way to use renewable energy, help our community, and contribute to our bottom line.†NewAge partnered with California-based Borrego Solar Systems Inc. for design and installation of the system. More than 4,000 solar panels were made by SolarWorld USA of Hillsboro, OR, for the rooftop system. “We wanted to work with US-based companies and use US-made parts,†said Baker. “We’re very pleased we were able to do that.â€
After roof upgrades in 2010, solar panels now cover three-quarters of the rooftop on the 244,000-ft2 building located in Southampton, PA. “It’s great to be able to do something so incredibly useful and green with the space on our rooftop,†Baker said. “Saving money on our electric bill is a bonus.â€
Getting Noticed: Separation/purification specialist Pall Corporation (known to our industry more by its “Pall Life Sciences†incarnation) is another vendor company that has openly committed itself to a sustainable future. Its commitment to partnering with customers for environmental sustainability has earned the company a place on the Cleantech Index (www.cleantech.com/the-cleantech-index-ctius) since 2006. The company offers products and engineered process solutions intended to enable customers to improve their responsible use of natural resources and minimize their waste streams. The Cleantech Index includes 72 companies that are considered to be global leaders in clean technology products and services.
In 2010, Pall completed an initiative to reduce its own energy consumption, waste output, and carbon emissions by 10% across the board. All Pall facilities worldwide are certified to the ISO 14001 international standard for environmental management systems (see the “Management Standard†box). The company is a member of the Carbon Disclosure Project (CPD), a global initiative to inventory greenhouse gas emissions, and the US Environmental Protection Agency’s Climate Leaders program, an industry– government partnership to reduce those emissions.
Eric Krasnoff, Pall’s president and CEO, says, “There is no greater calling for a fluid management company than helping customers protect people, the environment, and our natural resources. Together we are implementing technologies that purify and conserve water,
consume less energy, make alternative energy sources possible and practical, advance medicine, and minimize emissions and waste. Our collective efforts are enabling a greener, more sustainable future.â€
Selling the Concept: Some companies are specifically marketing “green†products to their customers. Mettler Toledo, for example, focuses on solutions for “green chemistry.†A webinar on the company’s website describes how Mettler Toledo’s laboratory products fit into sustainable pharmaceutical manufacturing through process analytical technology (PAT) and quality by design (QbD) (3). Case studies illustrate how those concepts are mutually beneficial. And Bayer Technology Services is showing how its online analytics can help reduce operation costs and improve sustainability through efficient use of energy and raw materials in cell culture production.
Meanwhile, SAFC entered into a marketing agreement this past summer with Stellar Biotechnologies, Inc. involving the latter’s good manufacturing practie (GMP)-grade high–molecular-weight keyhole limpet hemocyanin, an aquaculture-derived carrier protein with potential for conjugate vaccines. Stellar Biotechnologies is committed to environmentally sound aquaculture practices for sustainable cultivation of a renewable and long-term scalable supply of KLH and other proteins.
According to a DuPont survey, meeting sustainability challenges will require multiple strategies. Of respondents working on sustainable packaging, 65% said their efforts are focused on design for recyclability or use of recycled content, 57% are focused on weight reduction, 41% rely on renewable or biobased materials, and 25% say they are focused on compostable materials. “These results confirm that there are many pathways to improving packaging sustainability,†said William J. Harvey, president of DuPont Packaging and Industrial Polymers. “It starts with close collaboration throughout the value chain to spark innovation.â€
… And Contract Manufacturers
Speaking of packaging, fill–finish contractor Vetter Pharma International achieved ISO 14001 certification in September. The company’s environmental focus is reflected in its new center for visual inspection and logistics being built in Erlen, Germany.
“We are working on the sustainable development of our company,” says Thomas Otto, Vetter’s Managing Director. “That means linking economy, ecology, and social aspects in our daily work and future evolution. Through our management system for environmental, health, and safety, we have created vital structures and processes. They range from environmental management officers, ergonomic working conditions, and energy-saving production methods to the recycling of waste. That our system has achieved certification shows that we are on the right path. We will continue committing our resources to pursuing ever further improvement.â€
The new facility will harness renewable energy across its site: Vetter is installing photovoltaic cells on the facade to generate solar electricity. The company is also collaborating with regional farmers who run (exclusively for Vetter) a biogas plant used to operate a block heating and power plant within the company’s site. Geothermal energy will be used to regulate temperatures in the high-bay warehouse.
“Our new facility in Erlen combines efficiency and sustainability,†says Otto, “and its advanced processes support a high level of product and delivery security. Our investments in the facility and in renewable energy testifies to our commitment to the region.â€
Winning Ways: In 2010, chemical trade show Informex announced its first “Profiles in Sustainability†awards to acknowledge companies with demonstrated commitment to improving sustainability through current projects. The judging panel consisted of representatives from the American Chemical Society’s Green Chemistry Institute, the Society of Chemical Manufacturers and Affiliates (SOCMA), and trade media — who graded submissions on their scope and extent, benefit to the environment, and economic feasibility.
THE ENVIRONMENTAL MANAGEMENT STANDARD
The ISO 14000 environmental management standards series helps companies minimize how their operations negatively affect the environment; comply with applicable laws, regulations, and other requirements; and continually improve in those respects. This standard is similar to ISO 9000 (for quality management) in that certification is performed by third-party organizations rather than awarded by the International Organization for Standardization directly. In 2010, ISO 14001 was used voluntarily by >200,00 organizations worldwide.
For more information, see the source of this box (http://en.wikipedia.org/wiki/ISO_14000) as well as other online resources: the ISO website (www.iso.org/iso/iso_14000_essentials) and a free guidance manual from the National Center for Environmental Decision-Making Research (www.usistf.org/download/ISMS_Downloads/ISO14001.pdf).
“The purpose of these awards is not necessarily to pick winners, but to encourage sustainability among all companies,†Informex/UBM brand director Jennifer Jessup said. “The awards were born from a need to recognize that sustainable chemistry is not just a passing fad or a niche branch for the chemical industry.â€
Among the first winners were two familiar names to outsourced bioprocessing: DSM and Lonza. DSM was recognized for its continuous drive to embed sustainability metrics into process design and manufacturing — e.g., using process intensification for more effective scale-up, speeding up development, and driving down material costs. Green chemistry is important to such efforts. And since 2003, Lonza has run a technology initiative to introduce sustainable practices, using continuous processing and microreactor technology, to its business. Its microreactor technology platform supports rapid process development and continuous-flow production. It is robust and scalable: Projects have been run at multiton scale in a GMP environment. The system reduces waste and solvent use as well as energy consumption while increasing productivity.
DSM won again this year. The 2011 entries were judged on the 12 principles of green chemistry, the commercial scale and magnitude of their products/processes, and the uniqueness of their technology. “In essence, we feel that these companies are helping to set an example for the industry as we move toward a more sustainable future,†Jessup explained. “The judges chose the winning submissions by determining which organizations had best embraced the intention of the awards through thinking outside the box to produce innovative solutions with a high impact on the industry and a low carbon footprint on society.â€
DSM won for corporate commitment to sustainability as a business driver. This covers route-scouting services that lead to cost savings through identifying ways to streamline processes and provide clients with cost advantages, robustness in a proven scalable technology package, competitive advantage through intellectual property (IP) protection, and flexibility in implementation.
MARRYING “GREEN†CHEMISTRY AND BIOCHEMISTRY FOR A SUSTAINABLE FUTURE
Founded in 1997, the Green Chemistry Institute (GCI) is devoted to promoting and advancing green chemistry. In January 2001, it joined the American Chemical Society (ACS) in an increased effort to address global issues at the intersection of chemistry and the environment. Currently, 25 ACS-GCI international chapters are in various stages of development.
GCI put forth “12 Principles of Green Ch
emistry†in 2000 and “12 Principles of Green Engineering†in 2003 to help scientists and engineers designing new materials, products, processes, and systems. Bioprocessors should recognize and embrace many of these ideas. They are more than methods for addressing environmental problems; they encourage and reward innovation. According to GCI, one pharmaceutical company recently saved millions of dollars — and prevented millions of gallons of waste — through a process redesign using these principles.
Green chemistry is the design of chemical products and processes that reduce or eliminate the use and generation of hazardous substances. Much of the biotechnology industry’s drive toward progress came from and incorporates several of these principles.
Green engineering describes industrial processes that are economically feasible and reduce risks to human health and the environment. Again, many of its tenets should be welcome in biomanufacturing. They go hand in hand with fiscal responsibility.
For more information, check out the GCI website: http://portal.acs.org/portal/PublicWebSite/greenchemistry/index.htm.
“DSM is proud of its broad technological toolbox in chemistry, biology, and process technology and material sciences, which strongly contribute to our leadership position in sustainable manufacturing,†said Luca Mantovani, president and business unit director of DSM Pharma Chemicals. “Optimizing first-generation processes by driving down the cost curve is crucial for the commercial success of pharmaceutical compounds.â€
Sharing Ideas: CMC Icos Biologics vice president of manufacturing, David Wolton, has presented at several meetings on sustainability topics, from reducing carbon emissions from cell culture facilities using contained processes to reducing plastic waste from single-use technology. This reflects the company’s developing interest in this idea, which follows naturally from a commitment to continuous improvement and continual-flow processes (e.g., perfusion culture). Wolton has discussed assessing carbon footprints associated with liquid and preweighed media powders; new concepts of plant design (reducing size while increasing output); improved efficiencies through lean design of upstream, harvesting, and downstream processes. He describes how “buffer towers†can be used to mix media right next to bioreactors without danger of contaminating the room with powders. Based on equipment from Lormac Containment, Sartorius Stedim Biotech, and JM Separations, the tower concept uses disposables and isolator technology to facilitate those efforts — making it easier for companies to efficiently use lighter-weight, easy-to-store powdered media rather than buying heavy liquid media that take up a lot more storage space.
Big Pharma’s Big Initiatives
So-called green chemistry makes not only environmental sense but also economic sense. Product performance and cost-reduction are driving big pharma toward sustainability. The driver has until recently been more about “wallet green†then “Earth green,†but engineering groups are beginning to understand that both can go hand in hand.
Nigel D. Lenegan, cofounder and global chair of ISPE’s Sustainability CoP as well as Energy and Carbon Reduction Solutions Ltd., posted this comment in April 2010 to a blog on the subject:
“The obvious start point is HVAC, which represents probably 50–75% of a manufacturing facility’s energy use. With a clear facility operational assessment, the risks and benefits can be understood and measured against other quality issues. HVAC systems in these facilities have been over-designed for years, and it is time to correct this in both new and existing facilities. But these are complex areas with regulatory, product, process, and people constraints — so experience is essential.†(4)
The pharmaceutical industry overall has faced some challenges regarding sustainability, partly due to a prevalent batch-mode mentality, but also because until fairly recently “big pharma†hasn’t had the kind of financial pressures experienced in, for example, biotechnology. Twenty-first–century regulatory initiatives have begun pushing everyone toward lean manufacturing, process analytical technologies, and quality by design — all of which in the modern technological environment will almost inevitably lead to more eco-friendly processes. But there’s a lot more these companies can do — and are doing. The leaders tout sustainability initiatives in annual reports of such activities they make available online.
Building for the Future: ISPE has acknowledged top companies in this area with an annual sustainability award as part of the Facility of the Year program (www.facilityoftheyear.org) since 2009. The competition rules state that, “Winners exemplify the application of novel approaches, tools, techniques intended to improve effective use of energy, minimize waste, reduce carbon footprint, incorporate green manufacturing techniques, reduce environmental impact, and result in more efficient processing, utilities support, and business advantage.â€
The 2009 winner was Centocor Biologics Ireland (part of Johnson & Johnson’s biotechnology division, Janssen Biotech, Inc.). Back in 2001, Centocor began considering options to provide additional manufacturing capacity for two promising new drugs in its pipeline. With existing sites all built-out, the company had to start from scratch at a “greenfield†site. In June 2004, after three years of study, Centocor approved funding to establish a new cell culture and purification site in Ireland’s County Cork. The “BioCork†project’s overall goal was to get 180-kg/year biologic API ready to go by June of 2010.
With designers, architects, and engineers from The PM Group (a local firm) and CRB Consulting Engineers (from Plymouth Meeting, PA) and construction managers from John Sisk and Son (also local), the Centocor team worked closely with local residents to mitigate their large facility’s environmental impact on the community. They provided traffic mitigation alternatives, used advanced membrane waste-water treatment, captured rainwater for recycling, and installed a wood-chip–based biomass boiler for their base steam load. This project also involved extensive landscaping that included planting 70,000 trees to mitigate visual impact and air quality. BioCork is 40% more energy efficient than biotech facilities used as an internal benchmark, with a 90% reduction in its carbon footprint (compared with using fossil fuels). Through careful preparation, communication, and implementation of safety planning, this award-winning facility became one of the safest large projects ever built in Ireland. And thanks to integrated budgeting and scheduling coupled with full user participation, this complex project was completed ahead of schedule and under budget, and it exceeded capability requirements in all areas, particularly sustainability.
LEED GOLD CERTIFICATION FOR A BIOMANUFACTURING CLEANROOMBY JOHANNA C. JOBIN AND MANI KRISHNAN
At EMD Millipore, life-cycle assessment (LCA) studies revealed that the manufacturing of single-use products could be a significant contributor to global warming. As part of its sustainability strategy, the company wanted to identify initiatives for reducing related environmental impacts. The LCA results led it to focus on cleanroom operations as a way to reduce overall environmental impact.
Capacity Demands Drive Sustainability Initiatives
As demand grew for single-use assemblies, cleanroom operations at EMD Millipore’s Danvers, MA, facility couldn’t handle the increased manufacturing volume. So the company decided to renovat
e an unused warehouse and manufacturing space on that campus into a new cleanroom and support areas in accordance with the LEED (Leadership in Energy and Environmental Design) green building rating system developed by the US Green Building Council (USGBC, www.usgbc.org).
The LEED certification program is an internationally recognized rating system verifying that a building is designed and constructed to deliver improved environmental performance, from energy savings to water efficiency and improved indoor environmental quality. Projects receive points for activities in those categories and must amass a sufficient number of points to achieve LEED certification. Following the LEED-CI (Commercial Interiors) standards, EMD Millipore obtained LEED Gold status for this cleanroom project with certification points for use of recycled and preferred materials, lighting controls and occupancy sensors, and sustainable site benefits.
Recycled and Preferred Materials
More than 77% of all construction waste was recycled: bricks, cement, steel, and gypsum board. This was a challenge because the space had previously been used for storing flammable chemicals, so it had densely constructed walls, brick, mortar, and special blow-out panels that had to be demolished. The company used materials emitting low volatile organic compoounds (VOCs) in adhesives and sealants, paints and coatings, carpet systems, composite wood and laminate adhesives, and systems furniture and seating.
Energy Use
Running a heating, ventilation, and air-conditioning (HVAC) system in the cleanroom was flagged as having significant global warming potential. As a result, EMD Millipore implemented a unique particle-counting and air-handling system that reduced energy use by 69%.
In most cleanrooms, fans run constantly — whether manufacturing is taking place or not. To improve upon that, the company installed particle counters in cleanroom return air walls that constantly test the space. When the air meets cleanliness standards, fans can be slowed down automatically. On weekends — or other times when no products were being manufactured — fan speeds can be reduced as well, resulting in significantly energy savings.
With that change, the company recognized a savings of 141,000 kilowatt hours per year (equivalent to conserving 10,900 gallons of gasoline or removing 19 cars from the road for a year), which reduced its annual operating cost by US$16,000. The system cost about $12,000, so this initiative delivered a return on investment (ROI) in less than one year. EMD Millipore is now considering implementing similar systems in our other cleanrooms.
Lighting Controls and Occupancy Sensors: This cleanroom project also received points for incorporating a special system that uses lighting controls and occupancy sensors. Segmenting the large production area into zones and using high-efficiency T5-HE lights reduced lighting power density >35%.
A Sustainable Site
The vacant 30,000-ft2 area that has now been transformed into a cleanroom, warehouse space, offices, and associated supporting infrastructure would have been expected to create about a 25% increase in energy use for the facility in which it is located. Data show that the real increase in energy consumption is only 5% due to these LEED initiatives. EMD Millipore has also seen a 28% reduction in natural gas used to heat the facility, and it expects similar savings on air conditioning. Improvements made during development of this new cleanroom — along with other energy saving measures the company has implemented — form the basis for its divisional goal to achieve at least basic LEED certification for all future building projects.
Johanna C. Jobin is sustainability programs manager (johanna.jobin@merckgroup.com), and Mani Krishnan is director of single-use processing systems (mani.krishnan@merckgroup.com) at EMD Millipore, 80 Ashby Road, Bedford, MA 01730;www.millipore.com.
To learn more about EMD Millipore’s ideas on sustainability — and how you can approach your own LCA — look for an upcoming article by Jobin and Krishnan (“Using Life-Cycle Assessment Tools to Reduce Environmental Impacts of Single-Use Systemsâ€) in BPI in the spring of 2012.
AN IT LEADER LOOKSAT SUSTAINABILITY
Randy Tatlock is customer development manager at Aegis Analytical Corp. In September, we talked about sustainability as his company was preparing for its annual “Discover†conference for users of its Discoverant data management software. A major focus of this year’s gathering was how IT can fit into sustainability initiatives.
BPI: What degree of sustainability is realistic to strive for in the short term — and long term?
RT: Making life sciences manufacturing processes more green is generally accepted these days as the right thing to do for the environment and important for long-term business sustainability. Some of our customers are switching to renewable energy sources and trying to decrease water and energy use in the short term.
The early stages involve getting a handle on what natural resources can realistically be conserved without sacrificing product quality. That requires gathering and analyzing data to identify opportunities, better understand processes, and find specific ways to eliminate energy waste and costs. Benchmarking and monitoring energy use can help companies determine and reach longer term conservation goals. The right information can help manufacturers prioritize green initiative projects, such as replacing inefficient equipment or expanding production at manufacturing sites where energy costs are lower.
BPI: What hidden aspects do companies tend to miss in such evaluations?
RT: Companies tend to operate in ways that are the easiest or most convenient, but not necessarily the cheapest or most optimal for the environment. Green changes generally oppose the natural, comfortable order that we call “normal,†so they are often met with at least some resistance. I think this organizational aspect is very often overlooked and can kill a proposed change. Project leaders need to take time to educate their colleagues to show the benefits of operating differently.
BPI: What role does corporate culture play in supporting the local environment — and what unexpected returns may come from such investment?
RT: Corporate culture is key. A company’s “attitude†toward the surrounding community is a major factor that reflects what’s going on inside the walls of the facility. A company that supports the local environment and clearly communicates the benefits will gain a lot of local support that can carry it through an unrelated crisis. Aegis provides customers with access to data that can help them be more transparent and prove that they are responsible corporate citizens.
There are unexpected “green†returns. For example, when a company starts looking for greener solutions to save energy, it may discover cost savings. Sustainable business practices are in the infancy stage now, but people are thinking about them and incorporating them into decision making.
I think many biotech companies may actually be leading in green manufacturing practices. The biotech industry is a relative newcomer to the manufacturing scene and has grown up in era of sustainability. So it’s more natural for such companies to “build it green†than for big pharma, which has to retrofit more traditional methods already in place. Biotech companies can be catalysts for the right environmental changes as they partner with big pharma organizations to get their products to market.
oration:none;background-color: #f7f7f7;color:#000000;” >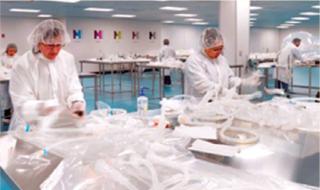
Over 20 years ago, Johnson & Johnson established its first environmental goal of reducing toxic emissions. Since then, the company has set and met a series of long-term goals addressing a range of environmental impacts. In January 2011, it defined the latest as “Healthy Future 2015,†both an extension of and departure from past goals.
The new program builds on previous environmental goal-setting and performance while incorporating social- and transparency-related priorities too. So the company is incorporating social goals and targets as part of its overall sustainability strategy — which is part of a larger trend that’s outside the scope of this report. Building on a legacy of reducing environmental impacts of its operations and products, J&J set the goal of partnering primarily with suppliers who embrace sustainability. The company wants to see venders demonstrating similar commitments through operations and goal-setting. Find out more online at www.jnj.com/responsibility.
The 2010 facility of the year for sustainability was also located in County Cork, Ireland. Pfizer Biotechnology Ireland built a pilot-scale facility for making monoclonal antibodies (MAbs) on a 29-acre site near the Centocor factory mentioned above. A small project team oversaw the full project life cycle: from early design to process validation batch production. With designers, architects, and engineers from Fluor Enterprises, Inc. (Greenville, SC) and local construction managers from Jacobs Engineering, Ltd., they built this facility using Pfizer’s green building guidelines and industry best practices for sustainability.
Some programs and features in this facility include extensive reuse of existing assets, waste minimization procedures, recycling as part of construction and operations, energy-efficient fixtures and equipment, and minimized air-change rates to meet both comfort conditions and classification standards. This phase 2b–3 clinical trial product facility was executed with an excellent safety record and delivered to a very aggressive timeline of 29 months from preliminary design to completion of operational qualification.
Pfizer won the prize again in 2011 for its Strategic Plant Restructuring and Energy Master Plan (SPRING & E-MAP) project in Freiburg, Germany. This included five major projects and a series of 200 minor projects that collectively enable the company’s packaging facility to operate with 91% renewable energy sources at a 30% energy savings.
Innovative technologies and automation are key factors in this success. Fully automated material flow systems, the latest multipurpose automation (enterprise resource planning, ERP) systems, and paperless order documentation were all components of Pfizer’s plan for increased cost effectiveness and sustainability. Computer-integrated manufacturing systems, Europe’s biggest wood-pellet boiler (which powers the plant’s air conditioning system by steam power), and state-of-the-art manufacturing concepts combined with process analytical technologies for a 15% reduction of production costs at the site. The office buildings are heated and cooled with geothermal power and photovoltaics, and laboratories and high-efficiency manufacturing areas are cooled through adiabatic means (5).
“The most impressive aspect of this project,†according to the judging panel, “is that it encompassed the engineering of a long-term sustainability program that is unparalleled in pharmaceutical manufacturing.â€
Clearly, the largest pharmaceutical companies have had the money to invest in the most aggressive and innovative approaches to environmental sustainability. And European facilities do seem to be leading the way, even if they aren’t all necessarily owned by European companies.
THE OUTSIDE PERSPECTIVE: A SUSTANABILITY CONSULTANT WEIGHS IN
Libby Bernick, PE, LEED AP, is vice president of TerraChoice, a sustainability marketing and consulting firm that combines science and business expertise to help environmental leaders build market share and accelerate progress toward sustainability. In October, I asked her about the pharmaceutical industry’s efforts in this area.
LB: Most corporate sustainability leadership has come from other industry sectors such as commercial building materials, consumer products, and electronics, with much stronger demand drivers and fewer product regulations.
BPI: What are some real economic advantages of going green?
LB: First, companies are using sustainability as a platform for growth. Sustainability leadership can be used to competitively differentiate in some markets or break into new markets. Large institutional buyers (e.g., Kaiser Permanente and Cleveland Clinic) are asking their suppliers about corporate sustainability initiatives, which creates business opportunities for companies with credible, authentic sustainability stories to tell. The other economic advantage of going green is operational efficiency. Reducing waste — whether energy, water, or materials in manufacturing and supply chains — will always boost the bottom line.
BPI: What about the trade-offs?
LB: The most important thing is that there can’t be any trade-offs in performance. When companies look at environmental trade-offs, they often miss opportunities by just looking at their own manufacturing operations. Most opportunities to create value are upstream or downstream of manufacturing operations and can be discovered with environmental life-cycle thinking. For example, one pharmaceutical manufacturer used life-cycle thinking to evaluate how product packaging is handled. It found some exciting redesign opportunities to use some reusable rather than disposable pieces in the distribution channel.
Another problem arises when companies focus on just one environmental hot topic. Today, many companies are trying to reduce their carbon footprints. Sometimes, this effort can unintentionally increase the water footprint. A company that uses certain plastics derived from conventional petroleum-based feedstocks (focusing on operations to reduce its carbon footprint) may actually increase the upstream water footprint. It’s important to look holistically at all environmental aspects so that you can minimize and manage risks.
BPI: How are companies comparing “apples to oranges†costs?
LB: One of the best ways is to use life-cycle thinking to help envision a product’s place in a larger system. Tools such as life-cycle assessment (LCA) and environmental product declarations (EPDs) help companies quantify all environmental impacts and costs from raw material sourcing all the way through to final disposal or reuse. Some are using these tools to compare single-use disposal with reusable options.
The challenge in using those tools is having the right data, and there’s a lot of effort involved in gathering the right information to estimate those costs and impacts. Another challenge is quantifying some of the more intangible risks, such as the continued availability of raw materials at reasonable cost. A
helpful approach is to profile and assess your supply chain using a supply chain sustainability benchmarking tool.
BPI: How are companies training employees in managing waste and encouraging them to submit ideas for lessening the overall carbon footprint?
LB: We are seeing companies use a wide variety of approaches. Waste-reduction efforts are often tied to lean or six sigma activities related to manufacturing operations. Successful approaches typically start with awareness building and education, followed by specific, discrete examples that employees can act on. If programs are not mandated from the top, often those that offer “carrots†instead of “sticks†are most successful.
Carbon footprint programs are very popular as a way to engage employees in sustainability efforts. Companies are using a number of tools such as on-line calculators or individualized sustainability programs on a company intranet site that employees can use to record and track their individual efforts. Another example is to promote regional efforts, with competitions and goals that provide longer-term incentives once the initial excitement about a program has worn off.
BPI: What lessons can biotech companies learn from attention paid to this topic by many leading vendors, service providers, and “big pharma†organizations? In my research, I find that those seem to be leading the way.
LB: The critical first step is to gather the right facts and build a business case to get executive level support for your sustainability program. Without that, you’ll have to proceed on a very different path. The other lesson is to develop a sustainability strategy that is customized to your goals, your market, and your business. A lot of companies make the mistake of just diving in and promoting whatever initiative their employees are interested in or whatever low-hanging fruit they can grasp. Although this works in the short term, it’s not a formula for long-term success.
The other important lesson we’ve learned is that you’ll know how far you still have to go only if you know where you are starting from. A great starting point is to benchmark and quantify your current sustainability performance and value proposition.
For more information, contact TerraChoice, 171 Nepean Street, Ottawa, Ontario, Canada; 1-800-478-0399; www.terrachoice.com.
Being Responsible:Corporate Responsibility magazine publishes an annual list of the 100 best corporate citizens across all industries. They’re judged on how they perform in several categories, including environmental responsibility and climate change, based entirely on publicly available information compiled by IW Financial. Familiar names that have ranked well on this annual list include Abbott Laboratories, Allergan Inc., Baxter International, Genentech, Genzyme Corp., Gilead Sciences, Johnson & Johnson, Life Technologies, Merck & Co., Pfizer, Schering-Plough Corp., Sigma-Aldrich Corp., and Wyeth.
The top-rated company in 2009 was Bristol-Myers Squibb. That highlighted its green initiatives including a solar panel providing 37,500 kilowatt-hours electricity annually (reducing greenhouse gas emissions); compliance with the LEED green building rating system (see the “LEED Gold†box) for its biomanufacturing facility in Massachusetts; and recycling of paper, cardboard printer cartridges, solvents, electronics, and so on. BMS also uses hybrid and high-mileage company cars and reduces land/air travel using “virtual†meeting technologies. Even little things can add up to big savings: Removing screen savers from all computers at US sites saved 1.9 million kW ($260,000) annually. And the company has been recycling the white Tyvec polyethylene jumpsuits from workers in sterile areas since 2000. In 2010, BMS was still ranked high in the corporate-responsibility top 100 at #7, and in 2011 at #4.
Baxter International was named 2011 Environmental Excellent Supplier of the year by Novation, a healthcare supply contracting company that serves 28,000 hospitals and clinics in the United States. Like many other big pharmas, the company published its sustainability annual report this past summer. Initiatives highlighted in the 2010 report include decreasing water use and net greenhouse gas emissions from operations and providing nearly $80 million in cash contributions, product donations, and grants to address critical global needs. Long-term performance goals aligned with each priority provide measurable targets and help the company assess its performance over time.
Bioprocessors Get It
It’s worth noting that two of the three ISPE sustainability facilities of the year so far have been biopharmaceutical facilities. Classical pharmaceutical manufacturing is a bigger waste generator than is bioprocessing — particularly when it comes to solvent use. Chemical synthesis requires large amounts of dangerous solvents and plenty of chemicals that come from the petroleum industry, whereas biological production usually requires more water. And as has been pointed out, the concept of “lean†manufacturing is a step toward sustainable manufacturing. Cutting waste is not only good for the bottom line; it’s also good for the local environment and the planet at large.
Single-Use Technology: This year’s ISPE Facility of the Year program awarded its first honorable mention for sustainability to Shire HGT (a division of Shire Pharmaceuticals) for its Project Atlas cell culture facility in Lexington, MA. The site manufactures Replagel and VPRIV enzyme-replacement therapies and will support future products now in development. Shire’s project extensively leverages single-use technologies at commercial scale. Driven primarily by speed to market, the company implemented a fully single-use upstream process technology at the 2,000-L scale. It faced numerous challenges and technical adaptations in the process, from bioreactor agitation to single-use product-contact surfaces in centrifuges. The facility was delivered faster than a similar-scale traditional facility, with reduced investment. Its smaller size translates directly to lowered utility requirements.
Several studies have suggested that single-use technology does indeed improve a manufacturing facility’s environmental picture (6,7,8,9,10). But companies that implement disposables to a large extent face a new environmental question: How do we handle the increased waste from these consumables? There are several options, as John Boehm (bioprocessing business unit manager for Colder Products Company) and Mani Krishnan (director of single-use processing systems at EMD Millipore) presented at this year’s BPSA International Single-Use Summit. They pointed out that “single-use manufacturing with appropriate disposal can reduce overall energy, water, chemical, and cleaning demands at a lower carbon footprint than traditional manufacturing.â€
Options vary regionally for disposing of plastic waste in general, and some of them are better choices than others when it comes to bioprocessing. Sending it to a landfill is the cheap and obvious assumption — requiring only treatment with chlorine dioxide or another kill method — but not only is this an environmentally unfriendly idea, it may be restricted or unavailable in some areas. A more extensive form of treatment involves grinding and autoclaving, which does reduce the volume of waste produced if not the mass. Many hospitals and research institutions do it, but it can be costly and still ends in a landfill. Incineration is widely accepted and reduces both volume and mass of waste, as well as toxicity, but even though it’s used for hazardous materials it may be legally restricted and expensive. It can also produce greenhouse gases. Cogeneration burns
waste locally to make heat or electricity for your plant. That’s a step up the sustainability ladder, but it requires significant initial investment and can also be legally restricted.
What about recycling? Is it even possible with plastics that have been used in bioprocessing? Most people in the industry currently say no. These components cannot be easily disassembled and tend to be made of mixed polymers — not to mention the biohazard potential. But one company is offering pelletizing to “upcycle†plastic waste into fuel. Sharps Compliance, Inc.’s Pella DRX process provides a relatively sustainable approach to deal with large quantities of viable waste, and EMD Millipore is piloting a product take-back program with its single-use customers.
Whether you’re looking to lower your carbon footprint simply through decreased business travel, improve your energy situation through efficiency or solar/geothermal/wind approaches, or lower your water/utilities use through implementing (and responsibly disposing of) single-use equipment, you may find your company is already on its way to a more sustainable future. Consider including environmental life-cycle assessment as part of your next project, and you may be pleasantly surprised at the results.
Author Details
Cheryl Scott is senior technical editor of BioProcess International. Facts and quotes not otherwise attributed come from company websites and press releases.
REFERENCES