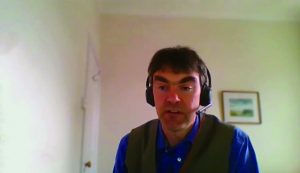
Charles Heise, PhD, senior staff scientist, bioprocessing and development, Fujifilm Diosynth Biotechnologies
Presented by: Charles Heise, PhD, senior staff scientist, bioprocessing and development, Fujifilm Diosynth Biotechnologies
Heise focused his presentation on the SymphonX single-use purification system and its role in continuous bioprocessing for the downstream processing of monoclonal antibodies (MAbs). He described how the system enhances the company’s MaruX continuous purification platform.
The company sought to meet the requirements of both batch and continuous processing, for which the single-use approach requires different flow paths, presents complex process integration across diverse vendor systems, and encounters limitations in dynamic operating ranges. The goal was to develop a flexible, standardized, and easy-to-use system to facilitate manufacturing. The SymphonX platform uses a single disposable flow path that executes different unit operations while providing advanced buffer management and integrated processing. The system’s fully disposable, irradiation-stable flow path and its mechanical and chemical stability are key features extending its operating lifetime in continuous operations. The system complies with USP Class VI for good manufacturing practice (GMP) use. The validated flow path, flow rates, and grading capabilities allow use in 100–2,000-L production scales for fed-batch and continuous processes. Standard protein-purification steps within the system use the same flow path, and each unit operation is controlled by an identical bioprocessing skid to simplify training, maintenance, documentation, and operator interactions.
Because the flow path is agnostic to the unit operation, the platform can operate using working buffers, buffer concentrates, and stock solutions. The proprietary buffer algorithm for just-in-time, in-line buffer blending or fixed-ratio, in-line dilution of buffer concentrates uses a four-way valve to deliver each buffer component into the flow path, generating gradients to specific concentration ratios. A proprietary static mixing chamber supplies a homogenous buffer into a unit operation. The control software complies with 21CFR Part 11, good automated manufacturing practice (GAMP) 5, and data-integrity standards.
Heise described use of the new platform with the company’s MaruX continuous MAb purification platform. The platform uses a perfusion-ready Apollo X Chinese hamster ovary (CHO) cell line in a 500-L single-use perfusion bioreactor connected to an alternating tangential-flow filtration (ATF) cell-retention device. Single-use technologies were used throughout the whole process to create an end-to-end, functionally closed flow path. The downstream process used an intensified batch purification strategy with high-column cycling and product pooling before final filtration and formulation — a semicontinuous approach to align control and validation strategies of current batch processes with advantages of intensified processing.
SymphonX devices on one side ran continuously and concurrently to process the perfusate, and on the other side, additional devices ran an integrated batch process. In the demonstration run, each setup used one flow path/lot (equivalent to six days of operation) and generated 3.25 kg of drug substance. Automation control used weight triggering to enable seamless transfer of product through the process with limited operator interaction.
Among the advantages shown by SymphonX within the demonstration run, the concentrated, premade buffers reduced buffer volumes from 14,500 L to 4,500 L, significantly decreasing the operation’s footprint. Data on process parameters and product quality illustrated consistency of quality attributes both upstream and downstream. For bioburden control, instead of controlling bioburden between unit operations, the team designed an aseptic boundary around the entire process using either sterile connections upstream and in the link to downstream or aseptic connections downstream. All media fluids and buffers were prefiltered using sterilizing-grade filters, and downstream consumables were sanitized with each use. The functionally closed flow paths demonstrated good bioburden control and introduced no contamination in the separate six-day demonstration lots.
The SymphonX single-use purification skid allowed for flexible, integrated, continuous bioprocessing through its multifunctional purification and buffer management capabilities. It operated seven downstream operations within the MaruX suite to demonstrate a continuous end-to-end MAb production run, producing 540 g of purified MAb per day.