Within the past few years, the single-use technology (SUT) arena of the biopharmaceutical industry has exploded in growth. Leading organizations have predictably and understandably stampeded to the “watering hole†of single-use to drink up the advantages that disposable components offer over traditional multiuse parts and technologies. The initial value and risk-reduction results are being realized — but not without the emergence of other trade-offs. End users continue to call for standardization in emerging areas of the industry while also recognizing challenges posed by trying to stay up to date with current standards.
How do we, as an industry, begin to tackle the job of staying current with standards and evolving technologies? Some regulatory agencies encourage the use of consensus for standardization, and single- use components suppliers and end users have slowly begun a process of harmonizing, collaborating, and standardizing. This is the perfect opportunity for the best and brightest in our industry to cooperate and share their time and knowledge.
When thinking about the hurry to use and manage new single-use technology, a comparative model may be one of a herd of elephants who visit a watering hole. Those giants seem to have figured out the value of cooperation. According to a study appearing in Bioacoustics Journal, when a herd of elephants is ready to leave the watering hole, one elephant vocalizes the plan, triggering a well- coordinated and collaborative dialog among the herd members. The lead elephant moves away first and gives a series of verbal and physical cues to the group. This well-choreographed “conversation†shows cooperation at a very high level. It displays the group’s ability to work together to complete a complex task. The same is true when they must band together to rescue one of the group’s calves from drowning in a watering hole. The mindset is not their calf or her calf. It’s our calf.
Elephants are considered to be a powerful and cognitively advanced species living in an organized society. Sound familiar? In the world of SUTs, we haven’t quite mastered the elephants’ knack for balancing competition, contribution, and cooperation. But we need to.
Who’s Drinking from the SUT Watering Hole?
A large number of bioprocessing end users and suppliers are regulars at the SUT watering hole. Organizations that write standards or guidelines for SUTs consist of qualified individuals from these very same companies. They are all our peers. We need to do a better job of capturing a picture of the current state. What’s possible? What’s needed? It is imperative that we, as an industry, set demands and then determine whether we can achieve those demands together.
SUTs are growing so fast in size and importance that the organizations that could help manage the chaos can’t keep up. It’s getting predictably crowded at the watering hole. Contributing to this problem may be factors such as company needs, regulatory requirements, market pressures, and cost. The best way to eliminate these problems is for all parties involved to become a part of the solution.
The National Technology Transfer and Advancement Act of 1995 directs the federal government to transition from developing to consuming industry standards established by consensus standards organizations. The law also encourages federal agencies to participate in voluntary consensus standards bodies when possible in an effort to reach agreement on best practices. Thus, the US Food and Drug Administration (FDA) has mandated the use of standards from accepted standards-writing organizations.
FDA Circular A-119 entitled Federal Participation in the Development and Use of Voluntary Consensus Standards and in Conformity Assessment Activities encourages the use of national and international consensus standards developed by the Center for Devices and Radiological Health (CDRH) for the industry of medical devices (not biopharmaceutical equipment). With government encouragement, the SUT industry itself would benefit enormously by making a collaborative effort to solve the problem before it becomes even more unmanageable. Now is an ideal time for our industry to establish single-use standards before federal agencies try to do it all for us.
A-l-p-h-a-b-e-t Soup
Many leading biopharmaceutical organizations (best known by their acronyms) have rushed to the SUT watering hole. SUTs have become less of a novelty and more of a coveted necessity in the quest for industry survival. Organizations such as the American Society of Mechanical Engineers– BioProcessing Equipment Standard (ASME-BPE, www.asme.org), the American Society for Testing and Materials (ASTM, www.astm.org), the BioPhorum Operations Group (BPOG, www. biophorum.com), the Bio-Process Systems Alliance (BPSA, www.bpsalliance.org), The Extractables and Leachables Safety Information Exchange (ELSIE, www.elsiedata.org), the International Society for Pharmaceutical Engineering (ISPE, www.ispe.org), the Parenteral Drug Association (PDA, www.pda.org), the Product Quality Research Institute (PQRI, www.pqri.org), and the US Pharmacopeial Convention (USP, www.usp. org) all have arrived at the watering hole. In the time that the SUT watering hole has been accommodating these groups, some positive signs of progress have slowly surfaced. Challenges still exist, however. How do we decide when novel becomes standard? Who decides it? Most people are calling for the standardization of SUTs. Although some groups have tried, it simply hasn’t happened yet. Why not?
One main reason could be that standardization has several different meanings. To some people, it simply means ensuring connectivity between components and uniform vessel dimensions. To others, it means a consensus body such as the ASME or ASTM publishing an industry- consensus method or specification that people will use and conform to develop the best and safest therapeutics. To most others, standardization, at the very least, means a minimum requirement and/or general guidance based on best practices and/or the current state of the industry. Bioprocessing is still a new and rapidly changing industry, which makes standardization complicated in its ability to stay current. Conformance may be perceived as a threat to growth and innovation. To some people, perception becomes reality.
The biopharmaceutical industry, at a minimum, is in desperate need of a standard set of single-use terms so that people can speak the same language about this technology. Two years ago, a paper focusing on model solvents entitled Standardization of Single-Use Components Extractables Studies was written by members of ISPE’s Disposables Community of Practice. The authors referenced the BPSA’s definition of extractables and leachables and proposed some common chemical solutions for the biopharmaceutical industry. If exposed to SUTs, those solutions should help scientists compare different SUTs and their potential risks to process solutions and drug products.
The article set off a debate that is still alive two years later. The focus of debate is whether those model solvents generate extractables or leachables, or something in between. BPOG has embraced the spirit of the paper and is currently working on its own formal approach to those model solvents. Other organizations also appreciate the concept — although disagreeing with some specifics — while openly acknowledging that the SUT community can do better. Through recent organizational efforts and collaborations, the SUT community has discussed the need to formally identify a set of model solvents and classify them within existing and well-established definitions used by USP and PQRI. It is clear that the complexity of single-use components and participants can complicate collaboration on the path to producing better and safer drugs. Future developments and implementations of new SUTs also would significantly benefit from development of shared information and a willingness from all organizations to communicate with one another.
History
The effort to produce the newsletter Single-Use News L-e-t-t-e-r-s began in 2013 as part of preparations for a town hall–style forum on single- use standardizations and best practices at the 10th annual BioProcess International Conference and Exhibition in Boston, MA. A panel of presenters represented many different groups working on documents to enhance SUT application in the bioprocess industry. The session was widely viewed as a success. All groups involved saw the value of maintaining an informal dialog to help coordinate the progress within these groups. They also shared an interest in providing general status information to the SUT community about each group involved as well as a desire to recruit members and volunteers to help move those efforts forward.
Following that first meeting in Boston, participants agreed to continue having regular teleconferences and public town hall meetings, as well as to publish a free bimonthly newsletter (Single-Use News L-e-t-t-e-r-s). The newsletter includes updates on SUT-related activities of the lettered groups along with summaries of town hall sessions and audience concerns. Six issues of this newsletter have been published to date.
Before that first town hall forum, a number of articles had been written on SUTs, and ISPE hosted a few sessions on standards during their annual meetings (Figure 1). BPI’s 2009 article “Organizing the Organizations of Single-Use Manufacturing†clearly summarized the efforts of SUT-pertinent organizations, showing unique perspectives. That was the start of the organizational “cross-fertilization†to help advance the SUT industry. Other articles have been written, and five town hall meetings have taken place since September 2013. The next town hall forum will take place in Huntington Beach, CA, at IBC’s Biopharmaceutical Development and Production (BDP) Week conference, March 30 – April 2, 2015 (Figure 1).
Compare and Contrast
Such efforts have proven that the key for all these groups is to understand one another. It is important to note differences between them and to appreciate all organizations and how they work.
Membership in each organization can be classified into one of two categories: corporate (e.g., BPSA, BPOG, and ELSIE) and individual (e.g., ASME-BPE, ASTM, ISPE, PDA, and PQRI). Of course the people within individual-member organizations represent their companies, but such representation is not as formal as for corporate- member organizations, in which their view may be more coordinated and valued. The fact that the charters of those organizations are structured in different ways can positively affect collaboration. Varying vantage points often combine to provide a more accurate picture of an issue.
As SUT use increases, it matures. User and supplier communities form their best practices and guidelines. Then the organizations formalize them into technical reports and other documents to enhance those guidelines and bring them to the next level of formality. The next stage comes when a consensus standards builds off of that progress. As use increases, requirements are added into standards. Those standards (along with all the others) are then used for reference by regulators and users.
Figure 2 shows the levels and relationships between the “lettered†organizations. There is interaction among all levels. But executing the interactions correctly to balance innovation and the maturity of technology is the trick. At the base, BPSA and BPOG (industry consortia) consist of corporate members representing corporations, end users, and suppliers. They have the flexibility to present best practices and publish documents. The next level consists of PDA and ISPE, which are industry organizations with individual members. Those groups publish best practice documents and technical reports that are routinely referenced by standards and compendial organizations as best practices.
ASTM and ASME are recognized ANSI consensus standards organizations. The FDA encourages use of these standards where appropriate. The characteristics of an ANSI standard include the following:
- consensus by a group that is open to representatives from all interested parties
- broad-based public review and comment on draft standards
- considerations of (and response to) comments; incorporation of submitted changes that meet the same consensus requirements into a draft standard
- availability of an appeal by any participant who alleges that these principles were not respected during the standards-development process.
The USP and European Pharmacopoeia (EP) are compendia organizations that develop standard testing methods required by law. Finally, on the top level is the FDA (and other regulatory agencies), which establishes laws and creates regulations for the industry. As noted above, in 1996 the US Congress passed the National Technology Transfer and Advancement Act (NTTAA) (PL104-113), which, according to the FDA’s website, directs “agencies to use voluntary consensus standards in lieu of government-unique standards except where inconsistent with law or otherwise impractical.†As part of NTTAA, the FDA is required to prepare yearly reports on the use of standards. As you move up through the levels of Figure 2, as you move up though this list, flexibility decreases while regulatory power increases. Conversely, as you move downward, regulatory authority lessens, but flexibility broadens.
In May 2014, PDA hosted a workshop at its headquarters in Bethesda, MD, entitled, “Single- Use Systems Cross-Organizational Workshop.†Twenty industry representatives and 10 FDA staff attended the meeting. Representatives from ASME, ASTM, BPOG, BPSA, ELSIE, PDA, PQRI, and USP attended and made formal presentations. The objective of this workshop was twofold: to promote a harmonized approach for supporting SUS activities within the industry (and in so doing to minimize duplication of efforts) and to communicate ongoing SUS initiatives among the group. PDA is committed to hosting the meeting again.
Each issue of Single-Use News L-e-t-t-e-r-s has a back page devoted to descriptions of these lettered organizations along with their contact information. So far, this effort has been primarily focused on US organizations, but we are open to participants from other organizations from outside the United States.
Collaboration and Alignment lead to Standardization
The industry is evolving, and progress is being made. SUT organizations now call each other. The same people who were attending multiple meetings are now asking others to sit in for them, or providing formal correspondence and updates of the other group’s activities. Formal cross- organization reviews of draft documents are beginning. It is all heading in the right direction, but more is needed in this important and fast-moving effort.
While many organizations are quenching their thirst at the single-use watering hole, questions are beginning to arise: Is there enough water? Is it getting contaminated? Who can’t fit in? Who is getting squeezed out? Who is going to tell someone when it’s time to leave? The answer to the lack of absolute cooperation may lie in the fact that many bioprocess industry organizations are made up of volunteers who work for companies that are in competition with those represented in other organizations. For instance, Joe Smith at ASME- BPE works for Bags-Are-Us, which is a competitor of Carol’s from the BPSA, who works for Best Bags USA. Some worry that standardization may compromise their competitive advantage. The desire to collaborate at the SUT watering hole might be hampered by that fact alone.
James Pauley of Schneider Electric stresses the business case for standards in his open letter to CEOs. He describes ANSI’s Standards Boost Business campaign, which is intended to leverage standards and conformance to win a trade advantage. He points out that “by participating in standards development, companies can influence technical content and align their products and services with changing market demand. They can gain insiders’ knowledge and early access to information on emerging issues, and can reduce redundancy, minimize errors, and shorten time to market. Businesses not only decrease the inherent economic risk of R&D activities by participating in standardization, they can also lower their costs by relying on previously standardized technologies.â€
When assessing the current state of biopharmaceuticals we must ask several questions: Where is the industry? What is the collective thinking? Where do we all want this to go? There is consensus that we all want drugs that are safe, pure, and affordable. We also agree that we are new, young, and just getting started. But we are not exactly sure of where to go. Some developments will help answer our questions, but those thoughts are still in the process of forming. If we’re confident about the current state, then we need to work with organizations to develop protocols.
The biopharmaceutical industry has thus far succeeded with its “pioneer†mindset. However, it has also developed the mantra of “if we didn’t invent it, we can’t reference it,†which is becoming costly and time consuming. We need to create an atmosphere in which each organization and individual learns from the others and builds upon that knowledge.
One way to do that is to compile standard definitions and the centralized ability to reference other industries such as medical devices and semiconductors. By borrowing or copying where we can, it is possible to prevent reinventing something (such as particle analysis, which is already well defined in both fields). The applications may vary, but the technology is the same. For example, for particle analysis technologies, a particle doesn’t “know†the difference in its applications. Think of it like this: If you needed to insert the same 950-word paragraph in four different places in a document, would you type it four times? Or would you type it once, then copy and paste it three times? The answer is a no-brainer.
The most recent town hall meeting on standardization of single-use systems took place at the BioProcess International Conference and Exposition in Boston, MA on 23 October 2014. The organizations took part in a face-to-face summit before the town hall forum to discuss specific opportunities for better collaboration among the groups. The groups came up with a detailed list of SUT-related topics each lettered organization is currently working on: leachables and extractables, SUT supply chain, change notification, change control, particulates in SUT, SUT system integrity, connectors, and SUT design verification. Table 1 shows which lettered volunteer organizations is doing work in those areas.
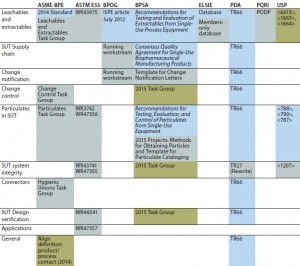
Table 1: Summary of what organizations are doing (blue = publishing, gray = in progress, green = 2015 Task Group)
Leachables and Extractables
Individuals participating in the town hall panels have discussed a need to separate the terms leachables and extractables because they are not always addressed in tandem.
The USP is developing three compendial standards: <661.1> for plastic materials of construction, <661.2> for plastic packaging systems, and <661.3> for manufacturing systems. To support these mandatory chapters, the USP is also developing chapters <1663> Assessment of Extractables and <1664> Assessment of Drug Product Leachables. The USP is currently revising chapter <661> specifically to address plastic packaging systems and their plastic materials of construction. This revision has been published for comments and the comment period has been closed. The USP is in the final stages of revising the chapter before making it effective and enforceable. Recognizing both the similarities and differences between packaging systems and systems used in pharmaceutical manufacturing, the USP is developing a section in chapter <661> that will address plastic systems used in manufacturing and their materials of construction. Because SUTs are plastic systems used in manufacturing, it is reasonable to expect that SUTs would be covered by this section. An expert panel (including members from BPSA, BPOG, PQRI, and ELSIE as well as experts from individual companies who are active in pharmaceutical manufacturing) was seated to develop this section and recently conducted its initial meeting in Washington, DC.
PQRI is developing Recommendation for Leachables and Extractables in Parenterals, which directly references USP and discusses data evaluation. Collaborative activities of PQRI participants from industry, academia, and government regulatory agencies have resulted in recommendations for threshold and best demonstrated practices for leachables in orally inhaled and nasal drug products. This guidance has provided manufacturers with a high-level strategic process to assess and qualify the safety of extractables and leachables. In 2009, a work plan was approved for extrapolating these concepts for parenteral and ophthalmic drug products (PODP) with considerations of a number of factors (e.g., dose, duration, patient population, materials, and product characteristics of PODP). The scope of the PODP project includes evaluation of materials commonly found in prefilled syringe systems, small- and large- volume parenterals, and ophthalmic/blow–fill–seal containers. Such principles of good science also can be translated to disposable systems in the absence of defined and specific regulatory guidance. Chemists and toxicologists are currently concluding research to propose methodology. A recommendations document is planned for 2015.
ELSIE continues to populate its safety database with safety information about extractables toxicology. The group also has prepared three papers on evaluation of results from a controlled extraction study pilot program, which are expected to be published shortly.
The BPOG Extractables team is working to make its user requirements and rationale more widely available. The team hopes its November 2014 article will clarify as many points as possible and help suppliers work within those user requirements. The BPOG team expects to release information on end-user practices for leachables this year.
BPSA has actively worked with BPOG in a yet unsuccessful attempt to produce a consensus document representing the interest of suppliers as well as users. The group continues to work closely with ASTM to develop a consensus standard.
ASTM has formed working group WK43975 New Practice for Determining and Characterizing Extractables used in Single-Use Applications. Their goal is to “provide a standardized approach for determining the most likely extractables profile from materials used in single-use applications, including [the chemicals, the conditions, and] the assays for these materials.†BPSA and ASME- BPE are supporting ASTM in this effort.
ASME-BPE is further developing its standard on leachables and extractables published in 2014 to expand more specific requirements for extractables testing, in accordance with ASTM WK43975.
ISPE’s annual meeting in 2014 focused, in part, on standardization of extractables/leachables assessments.
SUT Supply Chain
BPOG has made a CGMP expectations presentation to BPSA as well as a presentation at the BioProcess International Conference and Exhibition on the topic of supply chains in SUT. The group continue to conduct webinars and write papers on this topic.
ASTM’s biannual meeting in May 2014 included a workshop focusing on production and supply chain issues related to raw materials — predominantly single-use systems. Nearly 100 individuals representing end users, suppliers, and consultants attended this session. A follow-up to that meeting took place in October 2014.
Particulates in SUT
At BPSA’s July 2014 International Single-Use Summit, the group issued Recommendations for Testing, Evaluation, and Control of Particulates in Single-Use Process Equipment, which was developed by subject matter experts from both bioprocess suppliers and end-users. This informative document not only helps readers to characterize and quantify types and levels of particles in single- use systems and components, but it also recommends procedures for minimizing those types and levels. The document also offers a look ahead to what the industry should expect by way of improvements in particle control and how that control can protect the health and safety of patients. At this time, the biopharmaceutical industry still needs collaboration on the methods to detect particles in the SUT fluid path. BPSA has formed a task group to address those issues.
BPOG will be working with BPSA to close many aspects of the GMP expectations gap.
ASME-BPE’s 2014 standard contains several SUT-specific items including “Nonmandatory Appendix N.†The goal is to provide guidance to manufacturers and end users of bioprocess equipment that will allow them to develop and manufacture products and systems that meet particle acceptance criteria such as standardized hygienic union dimensions, steam-through connections, and product/process contact as it relates to system boundaries and facility design. The group is considering updating a standard that will reference the BPSA particulate paper. Looking ahead, ASME-BPE has initiated discussions with ASTM regarding testing protocol for particulates in single-use systems. ASME also has aligned its definition of product and process contact surface with ISPE’s new Baseline Guide in the 2014 edition.
ASTM’s work group WK43742 is writing a draft standard entitled New Practice for Characterizing Particulates Burden from Single-Use Systems.
The USP has issued acceptance limits for visible and subvisible particles. These limits can be found in chapters <787> Subvisible Particulate Matter in Therapeutic Protein Injections; <788> Particulate Matter in Injections; <790> Visible Particulates in Injection; and <1790> Visual Inspection of Injections.
Change Notification
BPOG and BPSA share the same position about the need to standardize supplier change notifications. The groups are forming a task group to define levels of change and to provide a standardized template for suppliers to streamline the change notification process and facilitate the implementation process for users.
ASTM is developing a change notification standard similar to E2500: Standard Guide for Specification, Design, and Verification of Pharmaceutical and Biopharmaceutical Manufacturing Systems and Equipment.
ISPE published an article in the May 2014 edition of Pharmaceutical Engineering entitled “Change Notifications for Single Use Components: Criteria from an End User Perspective.†It describes risk-based and science- based methods to catalog stages of changes in SUT manufacturing methods and raw materials.
Change Control
ASME-BPE will support its certification program and reference supplier change notification effort.
SUT System Integrity
ASTM created WK43741 New Practice for Testing Integrity of Single-Use Systems. It seeks to develop a standardized approach for SUT vendors to use throughout the life cycle of their SUT components. It is intended to help suppliers measure SUT system integrity on the basis of risk assessment and can be applied to all categories of SUT components.
BPSA has formed a task group to assist ASTM in developing a standard for best practices to test single-use bags.
USP chapter <1207> Sterile Product–Package Evaluation provides an overview of “leak test†methodologies (also termed technologies, approaches, or methods) as well as “package seal quality tests†useful for verification of sterile product package integrity. More detailed recommendations for the selection, qualification, and use of leak test methods are presented in three subchapters that address these specific topics: <1207.1> Package Integrity and Test Method Selection; <1207.2> Package Integrity Leak Test Technologies; and <1207.3> Package Seal Quality Test Methods.
At this time, there have been an increasing number of discussions about how to apply pressure/ rating to SUT.
Connectors
With stimulus and support from BPSA, ASME-BPE formed the Polymeric Hygienic Unions Task Group, which is similar to its Metal Fitting Task Group. (At this time, the industry is in need of SUT pressure/ratings, tube weldings, and hose barbs.)
SUT Design Verification ASTM produced SUT-specific WK46541 New Guide for Specification, Design, and Verification of Single-Use Pharmaceutical and Biopharmaceutical Manufacturing Systems and Equipment as a complement to the very successful standard for traditional equipment (E2500-07). The document is intended to be used by SUT suppliers, subsuppliers, and end users and takes into consideration the unique traits of single- use components and their rising popularity in the biopharmaceutical industry.
BPOG continues to offer consensus support to ASTM in the development of SUT design verification standards.
General SUT Efforts
ASME-BPE has formed many SUT-related task groups that will address the topics mentioned in Table 1.
In its 2014 Standard, ASME aligned its definition of product and process contact surface with ISPE’s Baseline Guide 7: Risk-Based Manufacture of Pharmaceutical Products.
BPSA published Consensus Quality Agreement for Single-Use Biopharmaceutical Manufacturing Products, which is intended to provide an example of common structure as well as to facilitate a dialog between suppliers and end users for quality agreements. Such a dialog should reveal the specific needs of end users and the many attributes of the quality system and operating mechanisms of suppliers, which in turn will provide the content for the final quality agreement between the two parties. In addition, BPSA is revising Component Quality Test Reference Matrices to include the addition of new sections as well as current topics such as filters, tubing, connectors, and bags.
ISPE’s Disposables Community of Practice (CoP) group is developing a comprehensive Good Practice Guide for Single-Use Technology. The guide is a practical go-to document that provides a road map for implementing single-use products. Authors of this document include end users and suppliers. ISPE’s CoP group reports that more than half of the sections in the guide have been written as a draft and welcomes authors who want to learn and share their experiences in for this project. The CoP group conducted educational SUT sessions at the ISPE annual meeting in October 2014 titled, “Single-Use Technology Can Give You a Fast Moving Scale-Up of Your Process, But Did You Miss Anything in the Frenzy?†Conducted in two parts, those sessions explored case studies and techniques concerning the best ways to embrace the rapid growth of disposables used in production processes in the most practical and efficient ways. ISPE’s annual meeting in 2014 focused in part on system design methods and a case study of single-use products in fill–finish applications.
PDA’s Technical Report No. 66: Application of Single-Use-Systems in Pharmaceutical Manufacturing was published in October 2014. PDA’s scientific advisory board, members, and staff are discussing the next steps in supporting the implementation of SUTs.
Website Resources
www.asme.org/products/codes-standards/bpe-2012-bioprocessing_equipment www.bioprocessinstitute.com/sus-newsletter.html www.bioprocessintl.com (article) |
A Place for All at the Watering Hole
We are starting to make progress at the proverbial SUT watering hole. The town halls, teleconferences, and newsletters all are helping this effort by fostering a collegial atmosphere both to ensure that all organizations are aligning and to confirm that we are identifying and managing all the SUT areas that make up that watering hole. But it is imperative that the industry set a course for standardization.
Readers are encouraged to research those organizations and find a place where they might add value to the SUT standardization efforts. The box “Website Resources†is a good starting point. Those with less expertise are encouraged to partake in volunteer opportunities to gain more knowledge and contribute to shaping the future of the industry. You are the qualified people who can write and proof these standards. There is plenty of room at this watering hole for everyone.
Acknowledgment
Organizational input was provided by Richard Levy, Kevin Ott, Robert Steininger, Jay Ankers, Desmond Hunt, Jim Bray, Tony White, Paul Priebe, Jerold Martin, and Diane Paskiet.
Corresponding author James Dean Vogel (jvogel@bioprocessinstitute.com) is founder and director, and Maureen Eustis (meustis@bioprocessinstitute.com) is a project associate at The Bioprocess Institute, 376 Dry Bridge Road, Unit H-3, North Kingstown, RI 02852. Single-Use News L-e-t-t-e-r-s is a central resource for information and updates on the expanding role of single-use technologies in the world of bioprocessing. It can be found at www.bioprocessinstitute.com/sus-newsletter.html.