MilliporeSigma has brought together its next-generation technologies, both acquired and developed in-house, under the formalized BioContiuum platform. The offering looks to obtain incremental process benefits now, with a mind to the continuous process of the future, the firm says.
MilliporeSigma’s BioContinuum platform, its self-described holistic approach to next-generation bioprocessing, is being launched at the AAPS event in Washington DC next week. Ahead of the event, Andrew Bulpin, head of Process Solutions at the vendor, told BioProcess Insider how the offering is the accumulation of MilliporeSigma’s response to industry’s needs, both now and in the future.
“MilliporeSigma’s BioContiuum platform will revolutionize drug manufacturing by setting the standard for improvements in process efficiency, simplified plant operations and consistency in manufacturing,” he said.
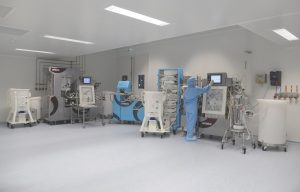
MilliporeSigma says its BioContinuum Platform includes process intensification technologies that provide incremental process benefits now, with a mind to the continuous process of the future
“We have been developing and acquiring technologies for the last several years as part of our next-generation processing initiative. We have reached a critical mass in our portfolio and the BioContinuum platform is the formalization of our next-generation offering.”
Biomanufacturers continue to look to increase speed, flexibility and quality, while decreasing risk and cost of goods. “The portfolio that we are announcing and rolling out over the coming months and years will help them achieve success in all these areas.”
By 2025, approximately 30 percent of the molecules within commercial manufacturing will utilize process intensification technologies, Bulpin said MilliporeSigma has estimated.
“The conversion of batch processes to continuous manufacturing is the future of the pharmaceutical industry, employing continuous flow, end-to-end integration of manufacturing sub-processes with a complex level of control strategies.”
Toolbox approach
MilliporeSigma describes the BioContinuum platform as offering customers a “toolbox approach” to biomanufacturing. When asked, Bulpin said such an approach forms part of the firm’s view that next-generation processing is an evolution, and that for now a “fully connected, fully continuous process is not necessary for customers to see benefits.”
“We have a history of helping our customer across the spectrum no matter where they are in the molecule pipeline. Whether they are conducting early stage process development at the bench or looking to implement new technologies when they run into issues in their clinical or commercial manufacturing stage.”
He added: “Our unique holistic approach to process intensification allows us to realize benefits of process intensification over the entire process, not gained by focusing on one area at a time.”
Pellicon Single-Pass Tangential Flow Filtration
Also at AAPS, MilliporeSigma is launching its Pellicon Single-Pass Tangential Flow Filtration (TFF) as part of the BioContinuum platform.
The tech is an ultrafiltration tool to concentrate product using a single pass through the membrane cassette without the need for retentate recycle as with traditional batch TFF processes.
“While this example of process intensification may seem focused on a particular step, downstream unit operations will see the effect of reduced product volumes for an overall increase in productivity and cost-efficient manufacturing process,” said Bulpin.
“Single-pass TFF with MilliporeSigma’s Pellicon filters is easy to implement and operate, offering manufacturers the flexibility to quickly mitigate in-process product volume challenges to meet their market demands without major capital investments.”