The US FDA has warned Japanese drug firm Takeda about its plant in Hikari, Japan after an inspection conducted last November.
According to a letter from the regulator, inspectors who visited the site identified a number of problems with the facility’s quality control unit.
The agency wrote, “Our inspection found that your Quality Unit (QU) did not take appropriate steps prior to resumption of aseptic manufacturing after a shutdown that included multiple significant activities that compromised cleanroom control.”
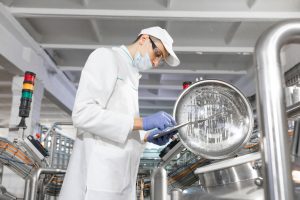
Image: iStock/Traimak_Ivan
It also said Takeda “failed to establish and follow appropriate written procedures that are designed to prevent microbiological contamination of drug products purporting to be sterile, and that include validation of all aseptic and sterilization processes.”
Black particles
The FDA also raised concerns about how Takeda investigates unexplained discrepancy and batch failures – specifically the detection of “black particles.”
It wrote, “For example, deviation report TW67805, initiated on August 23, 2019, did not include a thorough investigation of these recurring incidents.
“Although the investigation lacked a CAPA plan, you concluded that there was no product impact because the particles were easily detected since they settled at the bottom of the vials.”
The FDA said this approach was inadequate, because Takeda did not explain how it could “confidently rely only upon visual inspection to detect metal particles embedded in lyophilized cake.”
CAPA
Takeda confirmed receipt of the warning letter this week.
It said “The FDA made several technical observations about procedures and oversight.” The firm also said, “Patient safety is not impacted.”
According to Takeda’s website the Hikari facility makes active pharmaceutical ingredients (API), finished drug formulations as well as biological products.
A spokesman told us, “The Hikari Plant manufactures about 50 products, in several modalities: The FDA inspection was focused on the aseptic area.
“Following the inspection, Takeda immediately put into place a comprehensive corrective action/preventative action (CAPA) plan and has been providing monthly progress updates to the FDA. In conjunction with this CAPA plan, product supply is being monitored daily.
He added, “Our action plan includes remediation of the particles addressed by the FDA.”