Genmab says it chooses to outsource all its biomanufacturing having previously had its fingers burnt buying a facility in Minnesota, now owned by Takeda.
In early 2013, Danish drugmaker Genmab A/S sold its non-plasma-derived antibody manufacturing facility in Brooklyn Park, Minnesota, to Baxter Healthcare Corporation for $10 million (€8.7 million). The 215,000 square-foot plant housed 22,000 L of mammalian cell culture bioreactor capacity, and was originally acquired by Genmab from PDL BioPharma in 2008 at a cost of $240 million.
Genmab bought the Minnesota plant when it was in its “darkest days,” according to the company’s current CEO Jan van de Winkel.
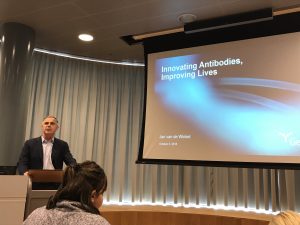
Genmab CEO Jan van de Winkel spoke during a press tour of The Netherlands
“It was an absolute mistake,” he told BioProcess Insider during a press tour of the Utrecht Science Park in The Netherlands where Genmab has an R&D center. “It was bought at a time when there wasn’t enough biomanufacturing capacity and it was very, very costly, and very inflexible.”
Therefore, when van de Winkel took the reins in 2010 his biggest task was to offload the facility and switch to an outsourcing model, essentially saving the firm from a financial crisis despite only receiving a fraction of what it paid PDL BioPharma, he added.
Baxter became Baxalta and sold the facility in January 2016 to Takeda for the planned manufacture of Entyvio (vedolizumab). (A week later, Shire agreed to buy Baxalta for $32 billion, and now with Takeda’s planned $62 billion takeover of Shire the plant has somewhat done the rounds and back again!)
Contract manufacturing
Since the sale, the firm has begun being profitable, and last year reported an operating income of DKK1,344 million ($208 million). This was aided by sales of Darzalex (daratumumab), a myeloma monoclonal antibody which clocked in sales of over $1 billion for Genmab’s marketing partner, the J&J subsidiary Janssen.
And now Genmab looks solely to contract manufacturing organizations (CMOs) for its production needs, van de Winkel said naming Lonza – who it inked a deal with to make its antibody-drug conjugate HuMax-TF in 2011 – among its many partners. The firm also relies on contract research organizations (CROs) for its clinical trials.
“We like to keep the brains inhouse, and the hands outside,” he explained. “Darzalex, for example, is manufactured for J&J by several CMOs at five different sites.”
However, he did note some frustration with third-party manufacturers in the occasional delays in securing space. “We like to claim more space [then we initially expect] at a CMO to avoid delays in production,” he said, adding more flexible CMO models are needed going forward.