Spirulina-based antibody developer Lumen Biosciences will convert a bakehouse into a biologics plant capable of producing 15 kg per week of cGMP-grade drug substance.
Seattle, Washington-based Lumen turns spirulina – protein-rich cyanobacteria touted by many health enthusiasts as a ‘superfood’ – into tiny factories that churn out therapeutic antibodies.
To support the development of its candidates, the firm has expanded its manufacturing footprint by leasing a former bakery in the Fremont-Wallingford neighborhood of Seattle.
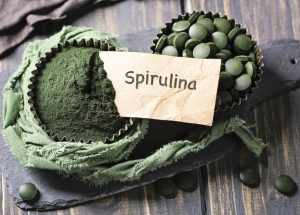
Image: iStock/egal
“All of our current products are grown in spirulina and delivered within whole-spray dried biomass, a food item that has been commercially distributed for decades in the US,” Lumen’s CEO Brian Finrow told BioProcess Insider.
Spirulina-based biologics
Engineering a food product to produce a biologic drug is not a new idea. Earlier efforts failed, mostly because it’s hard to produce enough of the biologic. If a patient must eat the equivalent of an acre of a crop a day to receive therapeutic benefit, it’s just not feasible as a drug. Spirulina has been grown at scale in the US since the 1970s, which means that it has a long track record and plenty of safety data. Furthermore, sprirulina is packed with protein so a little sprinkle goes a long way. The biggest challenge is figuring out a way to make those protein stores therapeutic. Antibodies are proteins. Lumen gets spirulina to produce them by engineering the cyanobacteria’s genome. But the company doesn’t use CRISPR or some other gene-editing technique, which would only make antibody production more complex and more expensive. The Lumen technology takes a gene that codes for a desired protein and inserts it into one or more designated locations in the spirulina genome. As spirulina grow and divide, they make the antibodies and pack them inside their cell membranes. Engineering also controls how much of a desired protein is produced in each cell. Spirulina only need water and light to grow. The spirulina that’s sold by grocers and health food stores is grown in outdoor ponds, then dried. Lumen produces its spirulina much the same way, though it does so in a controlled 20,000 square-foot-indoor facility in Seattle’s Fremont neighborhood. The end product is a greenish powder of dead, desiccated cells. Traveler’s diarrhea is Lumen’s lead disease target. The company aims to prevent the condition from developing in the first place. The Lumen drug, a capsule filled with the green powder, is intended to be taken by a traveler once a day. In the gut, the cell membrane breaks down, releasing its antibody payload. Those antibodies stand ready to bind to and neutralize toxic bacteria they encounter. The antibodies and pathogens are then swept from the gastrointestinal tract with bodily waste. In Phase I testing, the drug candidate was shown to be safe and well tolerated by patients. Lumen’s pipeline also includes candidates for norovirus and Clostridioides difficile infection, both of which the company aims to neutralize in the gut. There are no FDA-approved norovirus therapies or vaccines. |
“Those products are all grown outdoors in uncontrolled open ponds, so compared with the challenges those producers face, safe indoor production is very easy for Lumen. All areas of the facility to be used for manufacturing will be fully remodeled with modern floor and wall treatments, modernized electrical systems, and upgraded air handling.”
As well as removing the remaining commercial baking infrastructure, Lumen aims to make upgrades in the internal space to accommodate quality control activities.
“Unlike bread, of course, our cGMP-grade products are tested for identity and potency as part of the lot-release process. We will also be adding a clean-room facility for final fill/finish encapsulation activities,” said Finrow.
“The upstream and downstream processes are far simpler than the colossally expensive aseptic fermentation and purification systems used by traditional injection biologics makers. Specifically, the site will house large-scale photobioreactors and large-scale spray driers, which account for most of the capital cost.
“Because the spirulina are photosynthetic cyanobacteria, sugar feedstock and complex growth factors are not required and the media is extraordinarily simple—just water and salts, so media preparation is likewise very simple and inexpensive from an infrastructure perspective.”
Once renovation is complete, Finrow said that up to 15 kg of cGMP-grade drug substance will be produced per week.
Inhouse
The added premise is necessary to expand production as Lumen does not use contract development and manufacturing organizations (CDMOs).
“It was long appreciated that spirulina would be a very useful biomanufacturing host, but stable engineering was impossible before an inventive leap by Lumen scientists Jim Roberts and Ryo Takeushi. These patents formed the basis for Lumen Bio’s founding in 2017.
“The unique attributes of spirulina in turn now make it possible to develop biologic drugs in a photosynthetic manufacturing system for the first time.
“Because Lumen is the first to develop this new field, the CDMO industry does not yet exist so we must build it ourselves, exactly the same situation faced by Genentech and Amgen in the early 1980s.”
Pingback: From baking to bioprocessing: Lumen leases Seattle plant to advance ‘edible’ antibodies – Spirulina Digestive