Synthon Biopharmaceuticals chose to develop its antibody-drug conjugate (ADC) capabilities in-house to keep control of planning and product quality.
Aad Van de Leur, COO of Synthon Biopharmaceuticals, spoke at KNect365’s Bioproduction Congress in Dublin, Ireland this week on the need to adapt biomanufacturing strategies and technologies for next generation therapies, using his own firm’s antibody-drug conjugate (ADC) capabilities as an example.
“With the introduction of innovative high-potent biopharmaceuticals like antibody-drug conjugates (ADCs) the industry had to adapt and move to complete different strategies to produce these products,” he told BioProcess Insider, ahead of the talk.
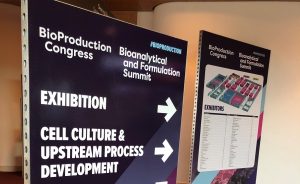
The Bioproduction Congress took place in Dublin, Ireland
“Next to the standard cGMP requirements additional safety aspects need to be taken into account. In addition, the volumes of these products would be limited resulting in smaller facilities and options to utilize single-use materials but also the need to adapt certain equipment.”
During the manufacturing of ADCs, solvents need to be used and this can hamper the utilization of single-use materials, he continued.
“Therefore Synthon put significant effort in leachable and extractable studies.” The results are being presented in Dublin, along with positive clinical outcome of a Phase I study in patient cohorts.
Homegrown manufacturing
Nijmegen, the Netherlands-based Synthon Biopharmaceuticals is a relatively small biotech, but he firm decided to invest in linker-drug, monoclonal antibody and ADC drug substance manufacturing facilities in-house.
“We believe manufacturing cost, planning and product quality can best be tackled when under own control,” Van de Leur said. “This is key in efficient and timely development of complex products like ADCs.
“However, working with high-potent products like ADCs puts much emphasis on safety for both employees as environment, resulting in complex clean room facilities including negative pressure, fumehoods and isolators. Our facilities have been inspected by regulatory authorities and partners and meet the standards to produce for clinical and commercial needs.”
More than 600 mammalian and microbial biomanufacturing decision makers and scientists have convened at the Convention Centre Dublin in Ireland to participate in KNect365’s Bioproduction Congress 2018. But following the £3.9 billion ($5.1 billion) merger of Informa and UBM the Bioproduction Congress will next year co-locate with CPhI Worldwide in Frankfurt, Germany.