With COVID-19 disrupting the supply chain, the advantages of inhouse manufacturing capabilities have never been so clear says CAR-T developer Celyad Oncology.
In 2012, Celyad Oncology – then known as Cardio3 BioSciences – received GMP certification for its a facility in Mont-Saint-Guibert, Belgium to support its allogeneic and autologous chimeric antigen receptor (CAR) T candidates.
Eight years on and in the midst of a pandemic, the decision to invest in internal manufacturing capabilities has never seemed so astute, says Celyad’s CEO, Filippo Petti.
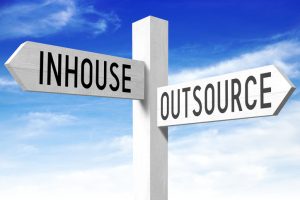
Image: iStock/3D_generator
“Manufacturing has slowed down in the industry but being able to produce from our own manufacturing facility has been a long-term benefit that,†he tells Bioprocess Insider.
Capacity has come to the fore during the past nine months as industry scrambles to secure manufacturing space to support potential COVID-19 therapies and vaccines. Projects have been moved out of some facilities to help speed through coronavirus programs, and there is talk of contract manufacturing organization (CMO) space being commandeered by coronavirus-focused projects.
The cell and gene therapy space was suffering from a lack of capacity before the pandemic, especially for adeno-associated virus (AAV), and the sudden arrival of potentially billions doses of viral vector-based vaccines has worsened the shortage.
“Having our own manufacturing facility allowed us to asses any risk in-house rather than rely on a CMO where risks could be delayed or exacerbated,†says Petti. “Also, by having in-house manufacturing we were able to stay on top of any potential delays and smoothly solve issues before they affected clinical trials.â€
He adds that, if given the opportunity, other advanced therapy developers should explore gong down an inhouse manufacturing route.
“Obviously transitioning manufacturing in house is a major step, especially for a costly product like a cell therapy, but the long-term benefits clearly outweigh the near-term difficulties and this has never been more apparent than during exceptionally challenging times such as what we’ve all experienced in 2020.â€
Petti’s comments reflect those made by other cell and gene therapy makers, including Pfizer – which has invested heavily in its gene therapy production network – and Astellas, which cited the appeal of gaining clinical and commercial manufacturing capabilities as a reason for buying Audentes Therapeutics for $3 billion last year.
Clinical disruption
While COVID-19 has affected the manufacturing side of the industry, Petti points out the clinical trials side has been hit particularly hard.
“The higher rates of COVID-19 equated to more delays with trials as getting patients to treatment and even recruiting patients became difficult due to strict hospital regulations that were quickly put in place to help protect workers and patients.
“Our clinical trials were also slowed down, but having trials at multiple geographic locations proved advantageous to continue enrollment despite outbreaks in some locations. For example, we were able to continue enrollment for the US while European sites were shut down and then reversed this enrollment once the US caught up to Europe with high COVID rates and Europe declined in rates.â€
He adds location for trials is now crucial, “especially for companies who might have sites in high pandemic areas, or in locations where the population is generally older and thus more at risk. Now, companies may choose to open trial sites in non-hotspot areas to avoid these delays in the future.â€
And unlike on the manufacturing front, Celyad is a believer that third parties can be a benefit in carrying out trials during these times.
“Having two CROs [contract research organizations] used for planning that are associated with different programs has also been helpful in keeping trials as ‘regularly’ scheduled as possible. Different CROs helps eliminate the risk of having all of your materials and work under one umbrella, especially if the CRO itself is impacted by the pandemic by either shutting down or slowing down processes.â€
Correction: The original article stated Celyad’s inhouse facility is located in Rochester, Minnesota when in fact the facility is in Mont-Saint-Guibert, Belgium. the firm had announced a site in Minnesota in 2015 but since changed plans.