Amgen’s commitment to next generation biomanufacturing has led to a reduction in its facility footprint of nearly a quarter since 2013.
In 2013, Amgen commenced a “company-wide re-engineering process” aimed at transforming its business to prepare for long-term growth. The restructure included significant job cuts and plans to reduce facility footprint by 23%, while ensuring increased bulk production through next-generation biomanufacturing platforms.
Five years on, and David Meline, Amgen’s CFO, said the firm has successfully transformed “the business “to achieve maximum speed, agility, and efficiency,” with next generation production, as seen at the $200 million (€175 million) Singapore facility that opened its doors in 2014, playing a major role.
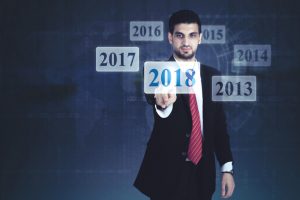
Amgen commenced an operational restructure in 2013 and says it has fulfilled all its commitments. Image: iStock/CreativaImages
“We’ve reduced our facility footprint by about 24% exceeding our target of 23% footprint reduction,” he told stakeholders on a conference call discussing end of year financials.
“Additionally, we’re embedding a permanent productivity capability into our business. We expect our productivity capability will continue to support disciplined cost management, contribute to funding strategic growth investments such as the 2019 investment in our early oncology programs and continued optimization of our operating model.”
Next gen biomanufacturing
The Singapore facility, which commenced commercial operations in 2017, differs from conventional biologics facilities due to its size and incorporation of enabling technologies.
The plant is equipped with single-use portable modular bioreactors (to a maximum size of 2,000 L), while processing takes place on a single level, rather than being segregated across multiple levels and operating suites. Meanwhile, media and buffer are prepared in a combined suite, while purification operations are conducted using portable and easily-configurable equipment.
The firm claimed it was constructed in half the time at approximately quarter the capital cost of a traditional plant, and the model has since been replicated for a similar facility in the US. Amgen broke ground on the $160 million Rhode Island plant last July.
Commitments complete
Meline added three other focuses of Amgen’s reorganization had also been fulfilled:
The 2013 reorganization also looked to achieve double-digit non-GAAP earnings per share (EPS) annual growth, $1.5 billion in cost savings, and significant improvement in operating efficiency.
According to Meline, these have all been achieved. Amgen reported a 14% EPS annual growth over the period, while the firm delivered $1.9 billion of annual savings versus the 2013 base. Thirdly, Amgen achieved a 15 point margin improvement in 2016, two years ahead of the commitment.
“We delivered on all of our commitments which positions Amgen very well for the next phase of its development. Looking ahead, we are excited to build on our recent transformation successes including maintaining and improving on our leading process development and manufacturing capabilities, driving our research and development innovation and continuing to build our market in global presence.”
For the full year 2018, Amgen reported total sales of $23.7 million, up 4% on the year prior. Net income too was up, with the firm reporting $8.4 million over 2017’s $2m.